Georgia Tech inventors have developed several modifications to probe microscopy and force spectroscopy techniques. One of the inventions disclosed is a class of sensors where a simple micromachined membrane structure is used to measure the tip displacement directly, and in a broad band manner eliminating the corruption of this information by the cantilever. Another disclosed technology involves the use of integrated large range electrostatic or piezoelectric actuators that replace the cantilever and the actuator that drives the cantilever previously described, with an integrated actuator which may have a much broader bandwidth. Additionally, for the first time, a complete FIRAT based Probe Microscope System has been disclosed to be used for material characterization, fast nanoscale imaging and imaging biological and chemical fluid samples.
- Optimization of the optical detection sensitivity in air or liquid
- Mini AFM configuration able to form images in very small volumes
- Multi-tip nanosensors with simultaneous, multifunctional capabilities
- Integrated actuator and a robust sensitive probe
- Life sciences
- Material science
- Semiconductors
- Proteomics
- Drug discovery
- Biomedical
- Defense
Most of the scanning probe microscopy (SPM) and atomic force microscopy (AFM) techniques rely on measurements of the deflection of a microcantilever with a sharp tip. Therefore, the resulting force data depends on the dynamic properties of the cantilever. This has limitations because cantilevers are resonant vibrating structures and provide only the related information. It is necessary to have the ability to rapidly scan over large samples while detecting forces to generate feedback signals. Additionally, there exists a need to increase the sensitivity of optical displacement detection as well as improve the design and fabrication process for the integrated force sensors for probe microscopes. Lastly, there is an unmet need for a complete system that uses Force Sensing Integrated Readout and Active Tip (FIRAT).
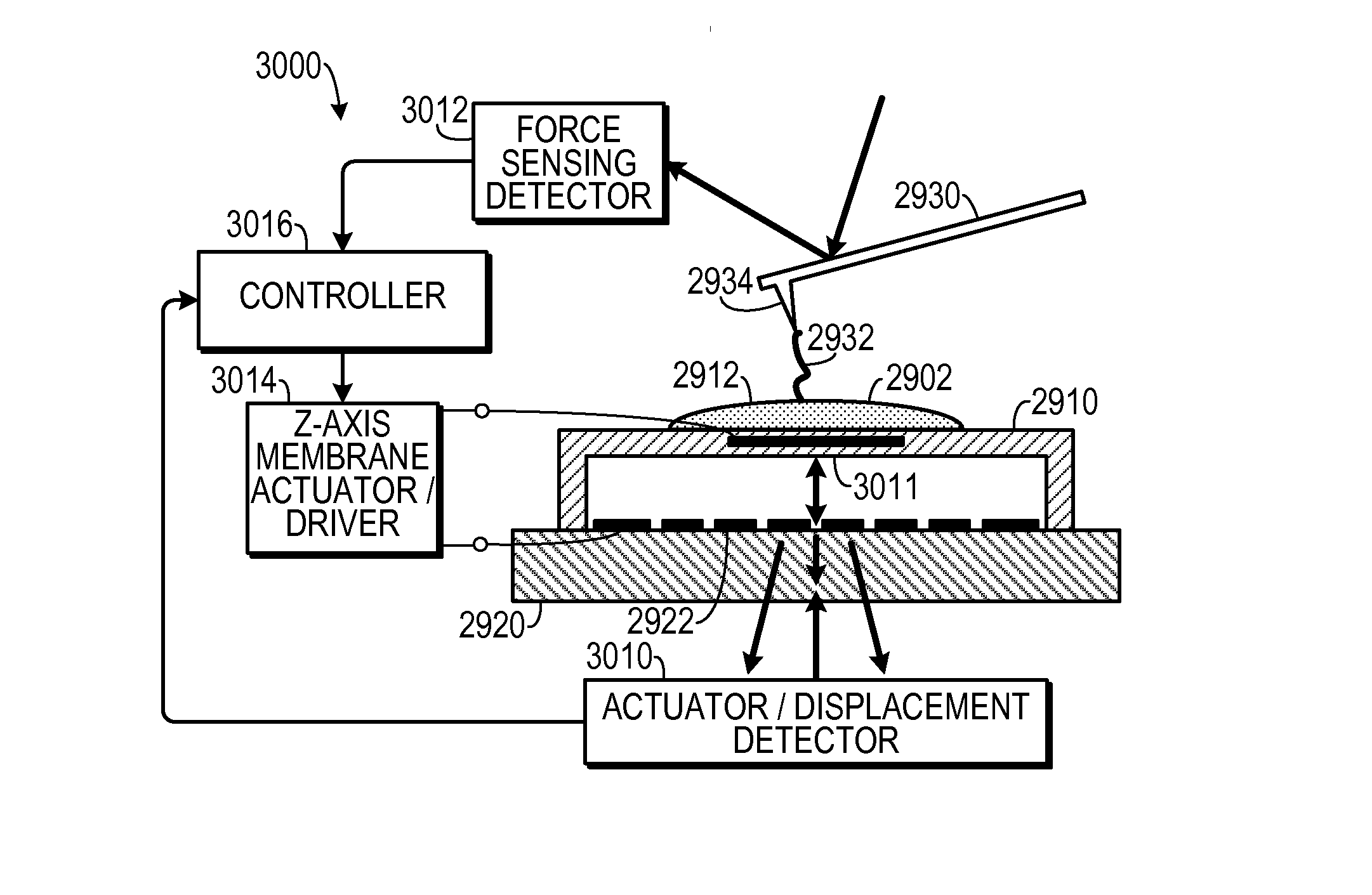