Homogeneous molecular catalysts enable reaction specificity, which is critical in drug manufacturing and other specialty chemicals. However, these types of catalysts are difficult to scale up due to complexities in final product separation and catalyst recovery. Heterogenizing these molecular catalysts, by attachment to a solid metal-oxide support, could transform the practical utility of molecular catalysts, simplifying catalyst separation and recovery to a filtering and washing process. Previous strategies to heterogenize molecular catalysts have suffered from reduced catalytic activity and leaching (loss) of catalyst, especially in environmentally friendly solvents like water.
Hybrid molecular catalysts increase recovery and decrease manufacturing costs
This approach to heterogenize molecular catalysts follows two steps: first attaching the catalyst to a metal oxide support and then encapsulating it with metal oxide via atomic layer deposition (ALD) to prevent molecular detachment from the surface. This versatile method can be used to attach nearly any type of catalyst molecule to an inorganic support because it does not require any specific chemistry. This new hybrid molecular catalyst exhibits unique reactivity compared to a variety of homogeneous and heterogeneous catalyst analogs.
Using ALD to create hybrid catalysts via immobilization of molecular catalysts (without concern for their homogeneous reactivity) opens up a new approach and chemical space for catalyst discovery. This new paradigm can improve the attachment and stability of molecular catalysts on solid metal oxide supports, making the catalysts easily separable from reaction solutions and recyclable for repeated use.
- Improved Reactivity: Attachment of molecular catalysts to solid supports can lead to new reactivity not seen under homogeneous conditions
- Reusable: At an optimal ALD layer thickness, the molecular catalyst remains highly active while still being resistant to surface detachment and subsequent deactivation
- Cost-effective: Catalyst separation and recovery is achieved via a simple filtering and washing process rather than energy- and time-intensive distillation or re-crystallization processes
- Scalable: In addition to the simple filter-and-wash process mentioned above, encapsulation requires only about 10 reaction cycles, making this process technologically and economically viable for large-scale manufacturing
This technology could have a wide impact across the chemical industry, including manufacturing of:
- Pharmaceuticals
- Agricultural chemicals
- Microelectronics
- Polymers
- Other specialty chemicals
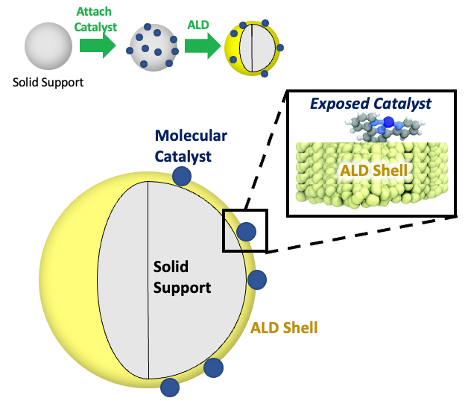
Figure 1. Depiction of process to attach molecular catalysts to solid support and then encapsulate on surface with a nano-scale atomic layer deposition coating.