Despite favorable performance for radiation attenuation, polyethylene and many other polyolefins generally possess lower tensile strength and impact toughness than high-performance polymer systems, such as poly(ether ether ketone). Reinforcing polyethylene and other composites can improve mechanical properties while adding beneficial qualities, such as electrical conductivity and oxidation protection that increases their suitability for a wide range of applications.
Reduced graphene oxides are a promising class of composite reinforcement materials due to their scalability and tunable properties; however, commercial deployment of rGOs is challenged by their poor solubility and tendency to aggregate. Furthermore, the potential economic benefits of rGOs are limited because existing production strategies impose restrictive processing requirements or energy-intense purification methods.
Chemically modifying reduced graphene oxides improves dispersibility in solvents and miscibility with thermoplastics
By chemically modifying reduced graphene oxides (rGO-dodecyl or rGO-dd) for high-density polyethylene (HDPE) reinforcement, commercially viable and scalable production is possible for a broad range of applications.
Typically, rGOs aggregate, which limits their ability to form homogeneous composites with polymers and renders them insoluble. This new approach uses a strong base and an alkyl halide to chemically bond with the undesirable functional groups left over from the exfoliation, oxidation, and reduction processes used to make rGOs. The rGO-dd product is easily recovered by adding methanol to the reaction mixture and then purifying via filtration. After purification, the alkyl chains prevent rGO-dd particles from aggregating, improving their dispersion in numerous solvents and their miscibility with many thermoplastics.
Two melt fabrication processes were developed. Melt compounding, in which rGO-dd material is blended with a polymer matrix, has demonstrated sheet resistances (RS) of 106 Ω-m at 10% loading of rGO-dd. The melt compounding option is suitable for conventional thermoplastic processes, such as injection molding or extrusion.
The second processing technique involves solvent casting (drop casting or spray coating) a dispersion of rGO-dd onto a thermoplastic and then thermally fusing the particles to form a robust coating. With this approach (which is not possible without the ability to form stable dispersions in volatile solvents) sheet resistances have been demonstrated as low as RS≈10 Ω-m, which far exceeds comparable anti-static coatings. These coatings are sufficiently conductive to not only provide static charge protection but also enable other active technologies, such as Joule heating, stress analysis, or dust mitigation.
- Reinforcing: The homogeneity of the composites enhances mechanical properties, such as tensile loading.
- Anti-static: Melt lamination results in a robust anti-static coating that is more durable than comparable polymer-based coatings.
- Conductive: This technology offers tunable conductivity suitable for a range of electronic applications, such as Joule heating, electromagnetic interference shielding, dust mitigation, and electronic tomography.
- Stable: The polymer and graphene layers are stable across a wide range of service conditions, including highly irradiated environments, without any loss of electrical conductivity.
- Customizable: Amounts of rGO-dd in the coatings as well as the specific binders/polymers and other components can be selected based on the desired properties. Additionally, coatings can be applied to the same substrate in varying thicknesses at different points and can even be used to build up three-dimensional structures on the substrate.
- Scalable: The easily scalable solution chemistry and purification/filtration make the process economically feasible, resulting in a commercially viable material for many applications.
Areas for use of these coatings are very broad and include, but are not limited to, space, military, equipment, automobiles, ships, buildings, bridges, civil structures, marine structures, and more. They include:
- Anti-static coatings for space, aerospace, high-voltage electrical cable insulation, oil and gas pipelines, household electronics, solar cells and batteries, explosives, or flammables
- Electromagnetic interference shielding for communications, measurement, and other precise instruments needed in space, aerospace, and more
- Joule heating for de-icing aircraft or spacecraft or for warming electronic components
- Non-destructive evaluation of components (by examining changes in electrical properties) for monitoring stress or damage to structural components of aircraft; turbine blades; or space applications, including space suits and habitats
- Dust mitigation in manufacturing, electronics, space, or other instances in which conductive layers are utilized to manipulate dust
- Protective coatings for resistance to:
- Corrosion
- Abrasives
- Impact
- Water
- Fouling
- Ultraviolet (UV) damage
- Electrical conductivity for fabrics and other materials
- Displays, including signage and flat panel displays
- Flexible displays, including light-emitting diode, organic light-emitting diode, and polymer light-emitting diode displays
- Lighting, including electroluminescent and OLED lighting
- Filtration membranes or biological scaffolds
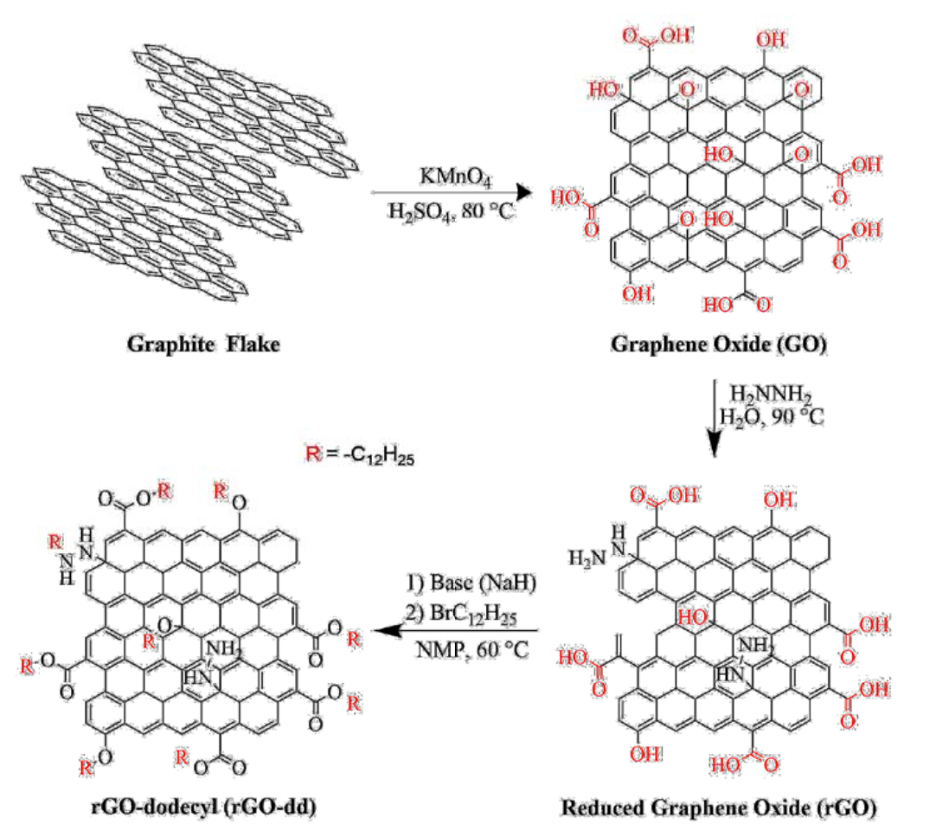
Schematic of rGO functionalization scheme to form rGO-dd. In this depiction, the process starts with commercially purchased graphite flake that is exfoliated using the Hummer’s method; however, the scheme is compatible with many rGO production methods. Functional groups in red are highlighted for clarity in following the reaction sequence.
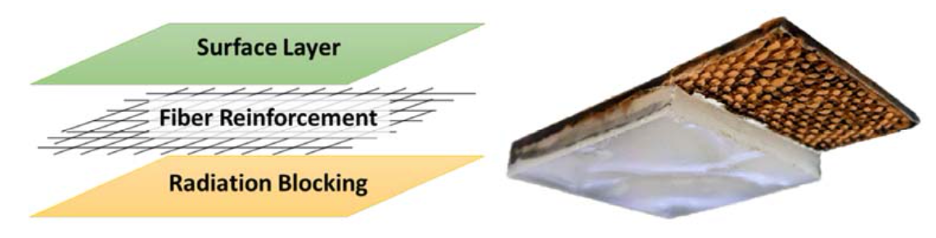
Schematic of multi-layer composite structure with distinct surface, fiber reinforcement, and bulk layers (left) with a prototype sample constructed of rGO-dd and HDPE as the surface layer with Zylon reinforcement and HDPE backing layer (right)