The Virtual Sensing Integrated for Predictive Reliability (VIPR) procedure combines artificial intelligence and machine learning (AI/ML) with vehicle sensor data to create virtual sensors throughout rocket hardware in places where physical sensors are not—or cannot—be located. Virtual sensing is conducted using deep neural networks to reconstruct sensors on rocket motors during controlled tests. The innovative process from Georgia Tech includes an algorithm that enables generation of new, verified, simulated data without the need for physical sensors during flight. Alongside a new hot-fire test facility, it aims to help further understanding of solid rocket motor propulsion, predict rocket performance, and provide multi-modal testing capabilities for maintenance, enhanced plume diagnostics, and predictive analysis on the entire solid motor system.
While initially developed for rocket test support, the underlying algorithm framework can be used for virtual sensing and predictive maintenance on trucks, airplanes, sea vessels, and other vehicles. VIPR is targeted at predictive maintenance and analytics to increase vehicle availability and reduce fleet downtime.
- Advanced: Acquires system data via virtual sensing, without the need for physical sensors in all desired locations
- Cost-reducing: Aims to reduce maintenance and planning costs for solid rocket motors and potentially other vehicle propulsion systems
- Predictive: Provides useful, repeatable, extensive data sets to predict rocket performance and enable proactive plans for propulsion system maintenance, upgrades, and replacements, potentially reducing downtime and failures
- Multi-modal: Offers enhanced plume diagnostics, predictive analysis, and simultaneous high-speed optical diagnostics
- Weight-reducing: Helps lower the total mass of aircraft and potentially other vehicles by eliminating or reducing the need for physical sensors
Georgia Tech’s innovation could be applied to virtual kitting of aerospace and other vehicle platforms, enhanced maintenance for deployed fleets, and vehicle/platform weight reduction. While currently targeting rocket-based vehicles, the innovation may also benefit:
- Aerospace platforms (fixed wing, rotorcraft, launch vehicles, uncrewed aerial vehicles)
- Fleet vehicles (big-rig trucks, oil rigs)
- Nautical vehicles (boats, submarines)
- Cars, sport utility vehicles (SUVs), and trucks
Virtual sensing and predictive maintenance provide the possibility of reducing downtime and avoiding failures in many applications, such as aerospace vehicles. Unfortunately, most sensors used for these tasks rely on real-time data to determine failures or remaining flight time—a reactionary approach based on limited data quality. Virtual sensing techniques can provide a better approach to predictive planning and reconstruction of missing data. Georgia Tech’s innovation meets this need with its AI/ML-based VIPR process. Used in combination with the hot-fire test facility, the technology is designed to provide multi-modal predictive capabilities in order to identify systemic issues and thereby isolate potential vehicle failures before they happen.
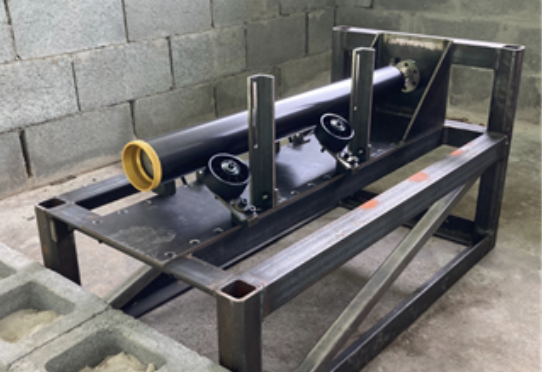
Georgia Tech’s hot-fire test facility.
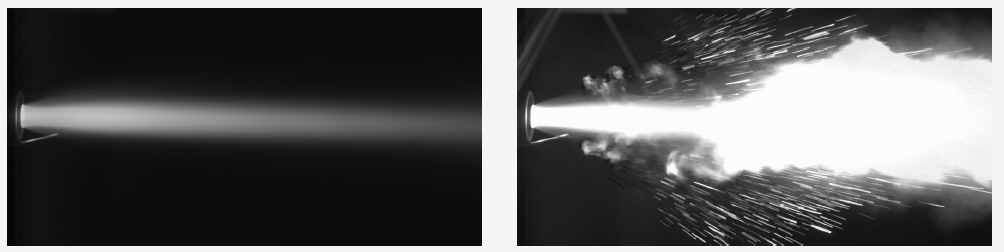
Flame analysis (top two frames) and shock detection (bottom four frames) are among
the capabilities of Georgia Tech’s VIPR process and hot-fire test facility.
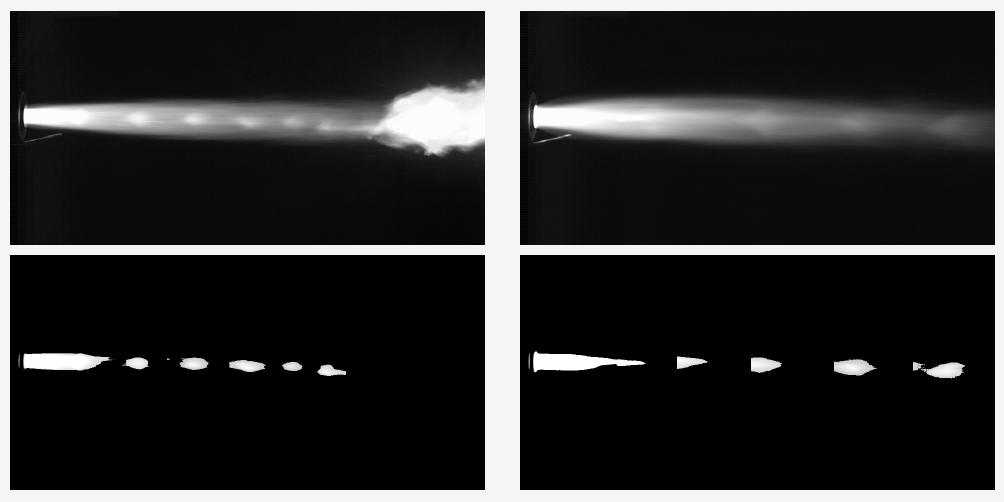