Current continuum robots lack rigidity control
Continuum robots can be used in a variety of tasks such as guidewires for interventional medical procedures, fruit picking in agricultural environments, and more. Within healthcare, the flexibility and dexterity for working in confined spaces and safely interacting with their surroundings has made continuum robots beneficial in surgical applications including neurosurgery; ear, nose, and throat surgery; and cardiovascular surgery.
However, conventional continuum robots lack the ability to actively vary the stiffness at discrete sections along the length of the guidewire and, as a result, the body of the guidewire can deform and move in unintended directions. In interventional medical procedures such as neuroendovascular and cardiovascular interventions, this control is particularly critical.
Variable designs offer selective actuation and stiffening along entire structure
This versatile continuum robot design offers stiffness control continuously along the length of a guidewire structure or at variable discrete locations along the structure’s length. Varying the stiffness can be done with mechanical, electrical, thermal, or any other form of energy.
One design incorporates external elastic elements such as compression or extension springs that envelope a guidewire and are placed along the length of the continuum structure. They are attached at each end to an annular plate, one of which is anchored and the other free moving. Three tendons are routed through holes in the fixed plate and attached to the free-moving plate to enable movement in three dimensions. Optionally, fewer tendons can be used to restrict movement to a specific plane. Multiple spring elements and tendons can be incorporated into a single guidewire to create variable sections of stiffness.
This design offers alternate approaches that can include using a machined outer tube (either continuous or sectioned), elastic elements placed inside the guidewire with the tendons routed along an inner lumen, or elastic elements attached between the fixed plate and the free plate that enable radial expansion and contraction that can lock the guidewire in place.
Another design uses electroactive polymers (EAPs) as actuators. Each EAP element is electrically isolated and connected to the fixed plate and free-moving plate— similar to the tendons in the previous design. The elastic elements can consist of a spring, electroactive polymers, shape memory alloys (SMAs), or combinations of those. For SMA-based elastic elements, the electrical pathways enable actuation by forcing the SMA to undergo phase transition upon heating, resulting in an elastic force to be exerted at the appropriate location along the length of the guidewire.
Using this approach, multiple elements can be incorporated into a single guidewire to create discrete sections of variable stiffness.
- Improved control: By varying the number, type, and locations of springs, EAPs, and tendons or electrical interconnects, flexibility and rigidity can be controlled along the full length or at any interval of the structure. Using three tendons enables three-dimensional control, while fewer tendons can be used to restrict movement to a specific plane.
- Improved outcomes: With better control of the wire positioning within a patient’s anatomy it may be possible to improve treatment outcomes.
- Decreased procedure time: Improved control and precision can decrease time needed to perform procedures.
- Versatile designs: The elastic elements can be placed along any section of the guidewire body and are not restricted to one actuator type along the length of the guidewire. Active stiffening can be achieved by a combination of actuating elements as needed for specific surgical needs.
- Potential applications in neurology, neuroendovascular interventions, cardiovascular interventions, urology, etc.
- Agricultural applications, such as fruit picking
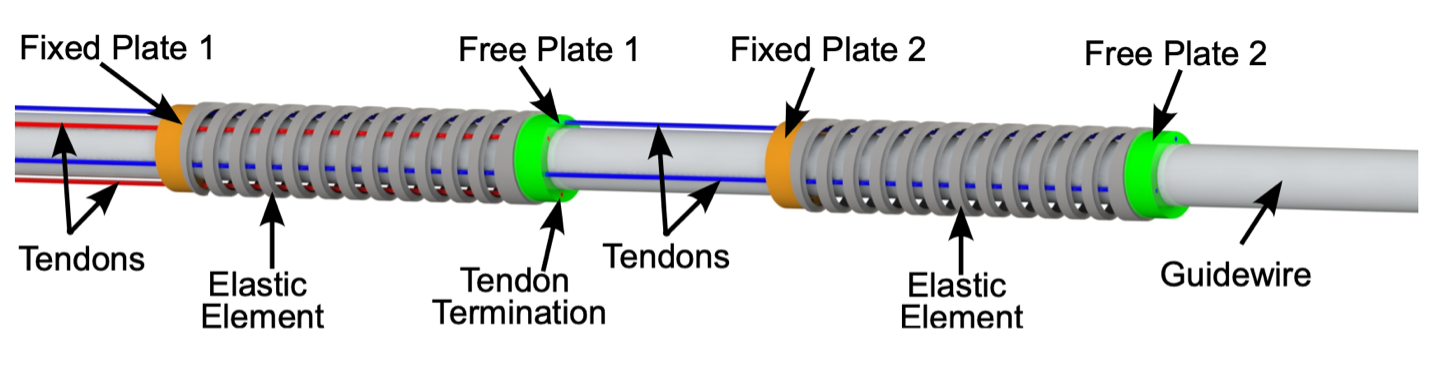
Example 1: Two compression springs are discretely located at two separate sections of the guidewire - combination of fixed plate and free plate at either end of the spring will enable tendon routing and termination.
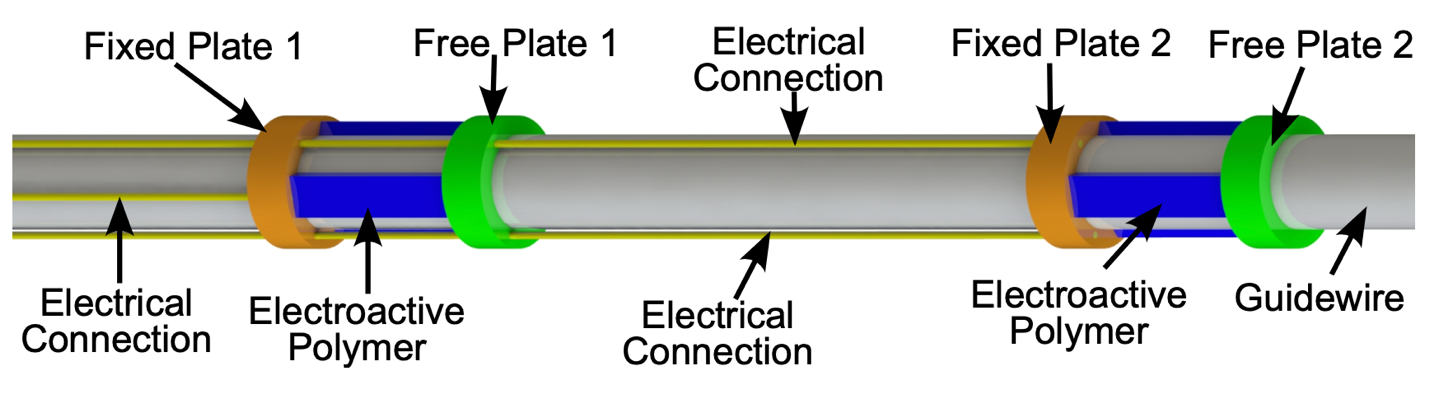
Example 2: A representative EAP element is shown at the location where stiffening is desired in the guidewire. The electrical wires would be routed similarly as the tendon(s)/push rod(s) to independently actuate each EAP element.