Georgia Tech inventors have developed and patented an ultrasound weld penetration depth measurement system that accurately and precisely measures weld penetration depth. This system is comprised of an ultrasound source, a sensor, and a signal processing system. The ultrasound source and sensor are placed on components welded together; the sensor detects ultrasound waves traveling through the material and sends the information to the signal processing system, which calculates the weld penetration depth. Because the ultrasound source and sensor can withstand harsh environments, this system has the potential to be used real-time during the welding process in addition to off-line, after welding.
- Real-Time – Potential to operate in a real-time welding environment
- Reliable – Test have shown repeated accurate and precise results
- Off-Life – Ability to check health and viability of welds
- Safe – Reduce risks of malformed and weak welds
- Economical – Prevents material from being wasted on weak and malformed welds
- Welding
- Safety Evaluation Checks
Welding is one of the most common techniques used to join components together. Currently, welds are tested after the welding process and are not monitored during the process. As a result, weak or malformed welds must be cut out and welded again or the entire component must be scrapped, wasting material. While full closed-loop control and automation of the welding process is being actively pursued to improve quality and increase efficiency, it is limited by the lack of accurate, high-resolution, non-destructive, and non-contact sensors that can be employed in harsh environments. Thus, there is a need for a sensing system that can measure weld penetration depth in harsh environments and provide accurate and precise information.
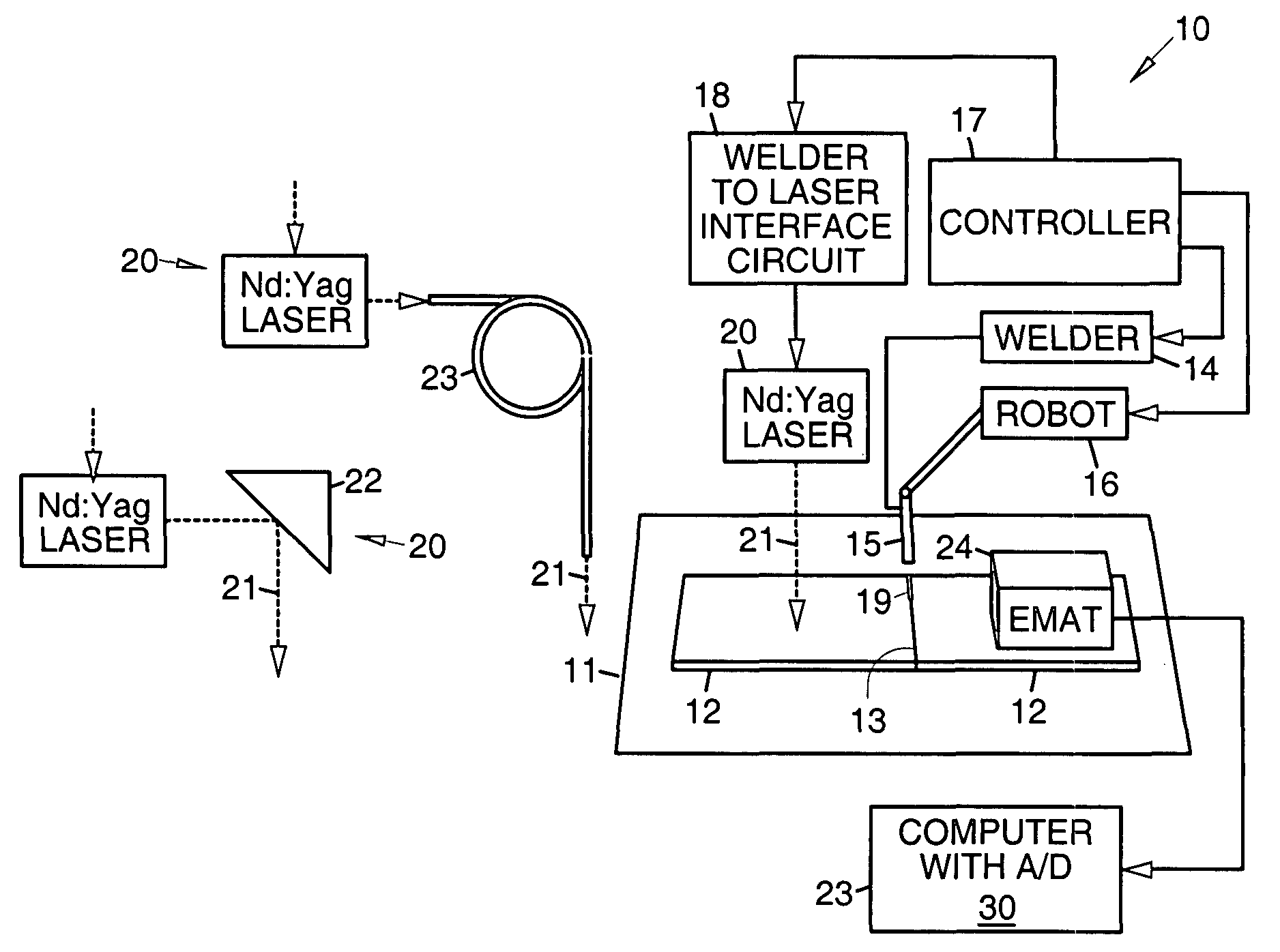