This unique thermal management system addresses cooling as a key challenge in electric vehicle (EV) motor design by dramatically improving torque and boosting power density capabilities for efficient, integrated cooling of high power density motors. Georgia Tech’s innovation surpasses the performance of typical single-phase liquid cooling with a two-phase embedded system that substantially increases motor heat rejection with a single unit. This in turn significantly reduces the size and weight of the motor and drive electronics.
The system’s unique design and performance open the door to new electric transportation options, such as electric trucks and buses (which have been slower to adopt electric motor technology compared with cars) as well as more electric aircraft options.
- High-performance: Utilizes three-dimensional silicon carbide packaging and novel drive topologies with reduced switching losses, leading to increased power density and lower motor system size and weight
- Embedded: Integrates with the motor and drive electronics rather than requiring an externally attached heat exchanger system
- Efficient: Dramatically increases volumetric heat removal rates in electric motor systems by employing a wick structure designed to assist liquid delivery to enable evaporative cooling
- Enabling and market expanding: Makes electrification of large transportation vehicles far more practical and may improve energy and economic security by reducing energy-related emissions and taking advantage of cutting-edge technologies
- Electric vehicles, including cars, trucks, buses, and aircraft
- High power density motor systems
- Electric traction motor systems
- Ultracompact in-wheel motors
- Motor systems for compact systems, including industrial equipment, pumping, heating ventilation, and air conditioning
High torque density motor systems typically used for transportation applications usually require separate motor, drive, and externally attached heat rejection units, resulting in large sizes and weights of the overall systems. This can be a barrier to their use in large power and torque density transportation and other applications. Lighter weight and more efficient cooling are challenges for these markets—and solving these should significantly expand the types of vehicles able to adopt electrification technology. Unfortunately, typical methods of integrating cooling in EV motor design fall short. Conventional designs usually employ single-phase cooling, such as an external water jacket, but the power and torque density produced by these motors are limited by their heat removal capability.
How It Works
Georgia Tech’s innovation addresses the shortcomings of other cooling methods with a two-phase thermal management system that can be embedded into the vehicle’s motor and drive electronics. Specifically, the technology employs wicks with micropillar pattens on polydimethylsiloxane (PDMS) substrates to enable thermal management of stator windings via evaporative cooling. It consists of a closed-loop, and coolant movement occurs due to a combination of capillary action of a motor slot liner acting as a wick, augmented with mechanical pumping. Adequate liquid supply is maintained within the entire microfabricated wick structure to achieve superior two-phase heat transfer coefficients. After removing heat from the windings, core, and rotor, the two-phase mixture is collected in an end cap and routed into a single air-side heat exchanger. The coolant is fully condensed within the heat exchanger and is pumped back into the wick structure for the motor.
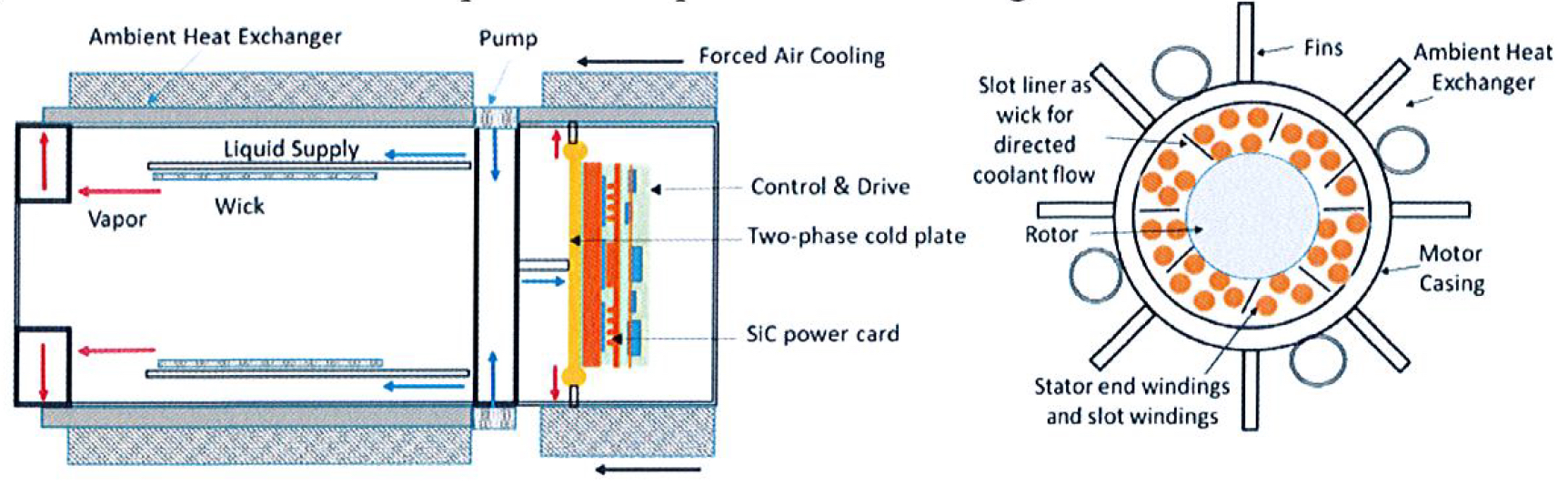
Georgia Tech’s evaporative cooling system includes co-packaging of interior permanent magnet motor and wide bandgap electronics with embedded two-phase thermal management. A closed-loop, wick-assisted evaporative system provides cooling of stator windings (left). The motor cross-section (right) illustrates the windings and a possible configuration of the ambient heat exchanger.