Georgia Tech’s patented reusable respiratory protection device is 3D-printed to custom-fit to a user’s face to potentially eliminate the need for fit-testing—an expensive and time-consuming task in health care and other workplace settings. The device includes a customized polymer frame that locks in to hold the filter media that provides the required degree of protection, including the 95% filtration efficiency characteristic of N95 respirators. After use, the filter media is discarded, and the frame is disinfected for reuse.
A user’s face is first scanned to create the profile and structure of the respirator-mask frame, which is then quickly produced via 3D printing technology. The form-fitting facial frame made of polymeric materials is designed to provide effective sealing around the face and prevent any face-seal leakage. Using 3D printing helps ensure a customized and effective fit that enhances device performance and comfort for the wearer.
The custom-fit device can be produced using a combination of material types, and the filter media can be made from various materials, structures, and manufacturing technologies depending on the degree of protection desired. Suitable elastomeric polymer materials for the frame include (but are not limited to) thermoplastic elastomers, styrenic materials, polyimides, synthetic rubbers, polyimides, and silicones. Removable filter media can include materials such as N95, N99, N100, R100, P100, and more.
Because the device is reusable, costs associated with acquisition, storage, and cleaning are anticipated to be one-tenth the cost of a single-use filtering facepiece respirator (e.g., N95).
- Aims to eliminate fit-testing: Designed to remove the expensive and time-consuming federal (i.e., OSHA) mandate for annual fit-testing for workplace use
- Improved fit: Adapts to fit specific facial features, increasing comfort and enhancing efficacy and potentially eliminating face-seal leakage to enhance performance
- Reusable: Withstands cleaning and decontamination
- Versatile: Accommodates a wide variety of material types, fabric structures, and manufacturing technologies
- Comprehensive: Significantly expands the range of users who can benefit from respiratory protection
- Environmentally sustainable: Reduces the quantity of disposable (and not easily biodegradable) N95 respirators discarded in landfills
This technology has the potential to transform the respiratory protection market and expand life-saving access to a wide variety of individuals and environments:
- Children to senior citizens: Individuals can have their faces scanned at hospitals, schools, or dedicated mobile scanning facilities then send information to 3D-printing companies for production.
- Customized filtration: A single frame can be used by an individual with the filter media changed to accommodate various environmental or respiratory health conditions.
- Varied workplaces: This innovation has the potential to significantly expand respirator use from health care settings to schools, offices, stores, and other workplaces, as well as in homes with immunocompromised or high-risk individuals being cared for by family members.
N95 respirators are designed to protect wearers from the transfer of microorganisms, body fluids, and particulate matter. Their successful deployment depends on factors such as fit, comfort, shape conformance, and durability. Current respirators are intended for a single use and fabricated from non-woven materials. They require fit-testing to ensure proper protection, a tedious and time-consuming process, particularly during emergencies, such as the COVID-19 pandemic.
This transformative Georgia Tech innovation has the potential to ensure proper and customized fit and eliminate face-seal leakage, leading to comfortable and cost-effective respiratory protection. The use of 3D-printing technology and polymer materials enables a reusable and novel approach to respiratory protection.
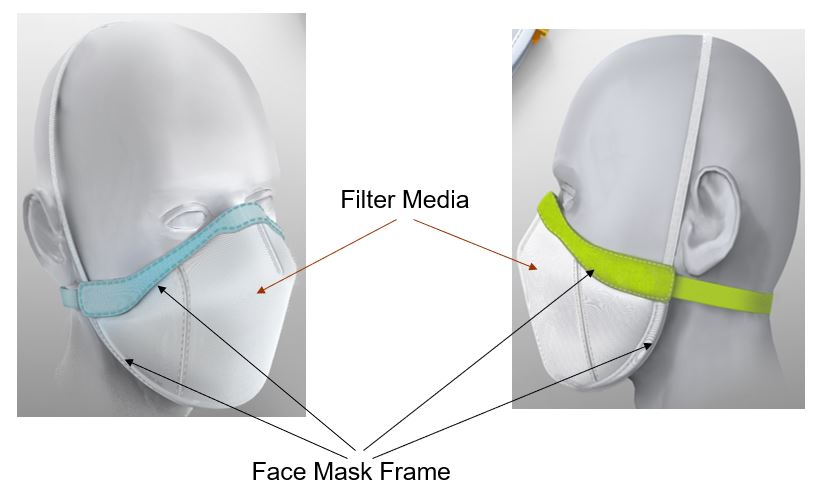
Conceptual representation of the face mask frame with filter media