Vehicles in storage will often not start due to dead batteries
Fleets of vehicles in long-term storage, particularly for the military, must be deployable at a moment’s notice. Often, however, battery health is insufficient to start a vehicle after being stored for extended periods of time. In addition to the delay in that vehicle’s use, the vehicle can block and prevent many others from being deployed when a fleet is stored in a warehouse.
Tracking the vehicle’s specific location in a warehouse is also important. Current tracking methods that rely on scanning radio frequency identification (RFID) tags are problematic when vehicles are moved during routine maintenance and not replaced to the same location. This results in errors in the vehicle location database and delays in finding specific vehicles.
Wireless system creates a network to monitor vehicle location and health
This vehicle health and location monitoring system consists of a central logging station, a battery monitoring system (BMS) device, and a handheld reader. The BMS device (see video and figures below) is used to scan the vehicle’s RFID tag and is then attached to either the vehicle’s NATO (North Atlantic Treaty Organization) slave port or the standard auxiliary port for commercial vehicles.
The system automatically establishes a self-accumulating mesh network of the installed devices. This network provides wireless connectivity for vehicle monitoring—whether performed by either a human, drone, or mobile robot—to check battery health, other vehicle health, or damage such as flat tires as well as to determine locations of all connected vehicles. The vehicle information is logged, continuously updated, and stored and/or transmitted to the central logging station or a handheld reader via Bluetooth®, Wi-Fi®, cellular, or satellite communications.
A technician, drone, or mobile robot can then locate vehicles based on RFID tags. By interfacing with the Georgia Tech Real-Time Intelligent Fusion Service (RIFS), data from a drone can be combined with the BMS data, creating a map of vehicle location and indicating vehicle battery health as well as any damage the vehicles have sustained. A mobile robot can also locate vehicles, sending real-time video and/or storing recorded video for later review by technicians.
Additionally, the handheld device includes a camera with optical character recognition (OCR) to identify a vehicle based on its vehicle identification number (VIN), serial number, or other identifying markings. This enables the technician to scan a vehicle’s ID to see its status on the handheld reader.
The BMS can also interface with the mobile robot for trickle-charging vehicles with low battery levels. For this functionality, a movable target is connected to the BMS at a point accessible to the mobile robot. The robot connects to that target, creating a charging circuit to the vehicle battery and safely charges the vehicle system. To ensure the BMS maintains power, the BMS includes a secondary rechargeable battery.
Watch this video for demonstration of the system in action.
Bluetooth is a registered trademark of Bluetooth SIG, Inc.
Wi-Fi is a registered trademark of the Wi-Fi Alliance.
- Maintains accurate locations: The system dynamically configures the mesh network, communicating with other units localizing themselves within 30 meters. A vehicle’s location can be pinpointed to within 10 meters and is continuously updated within the network to maintain an error-free vehicle location database.
- Clearly communicates vehicle information: When looking for a specific vehicle in a lot, the user is notified of vehicle proximity via the handheld reader’s haptic, audio, and/or visual feedback. A mobile robot transmits video as well as vehicle information.
- Enables battery charging: When a vehicle is found with low battery levels, a mobile robot can safely provide a charge to the battery to get the vehicle running.
- Identifies damage: In addition to monitoring battery health, when used with a drone, the system can identify vehicle damage, such as flat tires.
- Provides versatile connection options: Connectors fit commercial vehicles as well as comply with required NATO standards for power connectors for military use. Near-field communication (NFC) capabilities can replace RFID when needed, and an optional GPS/global navigation satellite system (GNSS) module can provide outdoor localization.
- Supports advanced control: A geo-fence functionality stops vehicle location reports when outside of a prescribed location.
- Provides large-scale functionality: This system can identify and track hundreds of vehicles at a time. When using Bluetooth Low Energy (BLE) mesh networking, thousands of devices could potentially be connected at once.
- Offers secure access: The system includes an advanced encryption standard (AES) for securing messages over the air as well as securing information in the vehicle database.
Vehicle location and health monitoring for:
- Military vehicle fleets
- Commercial vehicle fleets
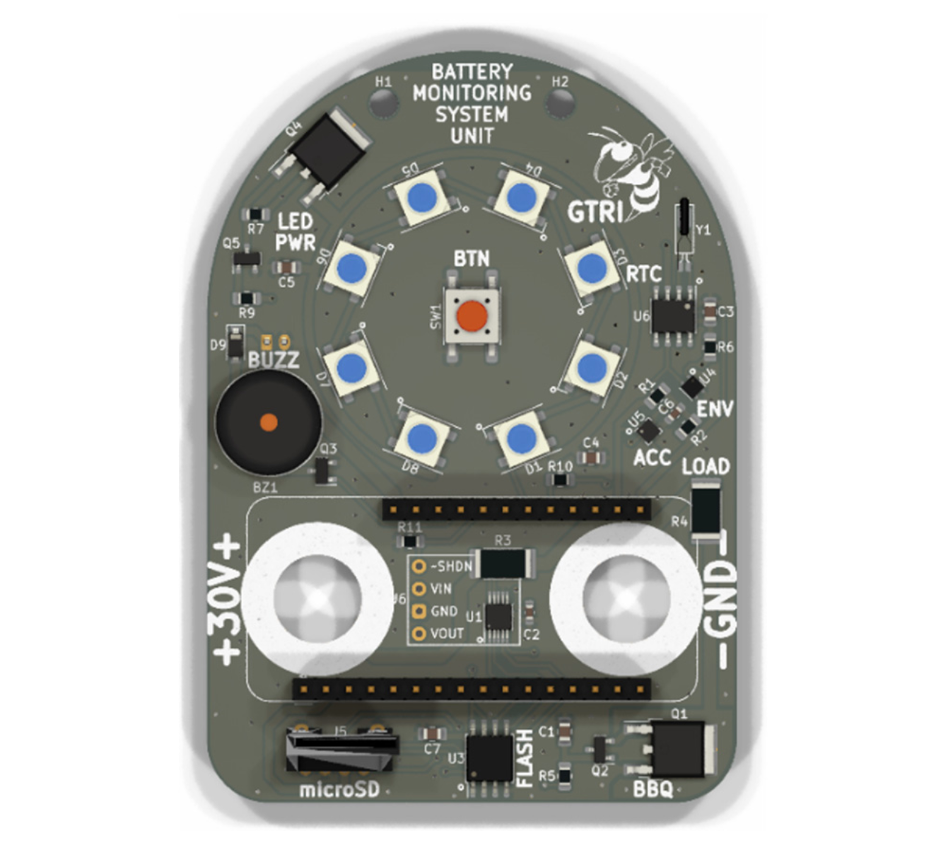
Front view of the BMS custom circuit board (military version).
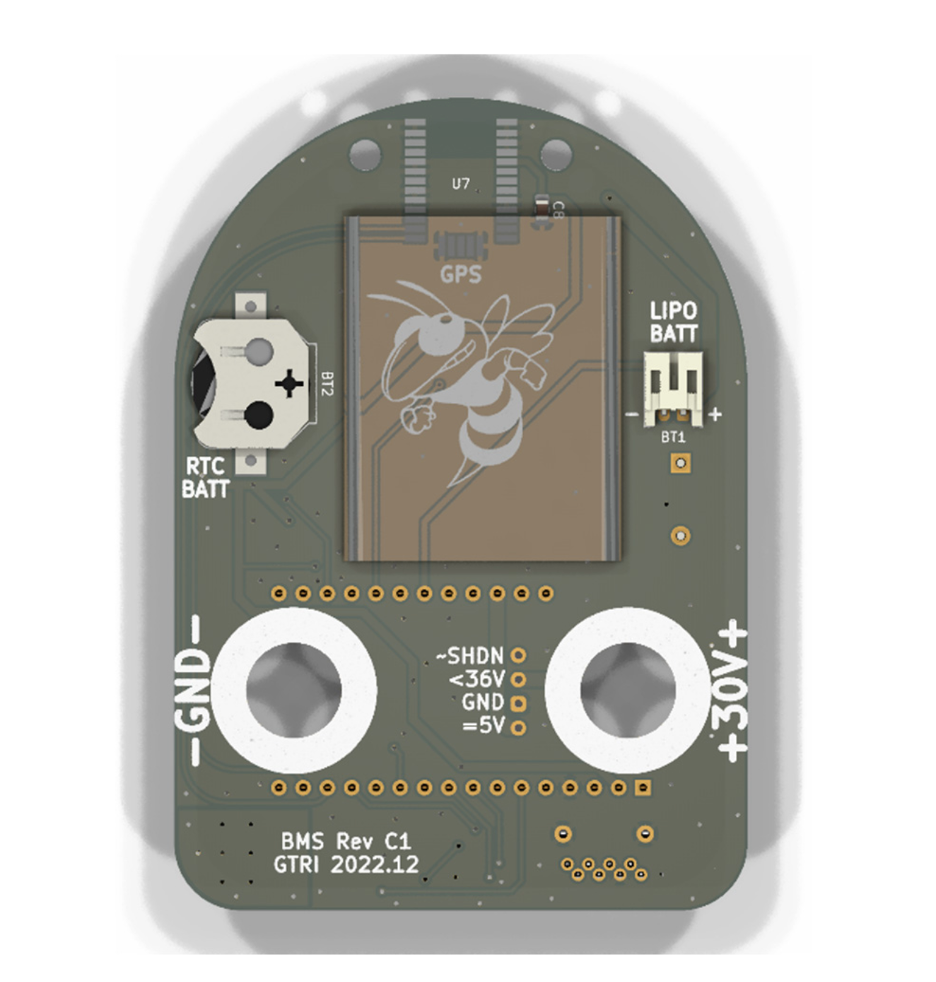
Rear view of the BMS custom circuit board (military version).