This processing technique strengthens single-polymer composites (SPCs) and makes it easier to mass produce them using conventional melt processing methods. SPCs are comprised of fibers and matrices that are made from the same polymer. When compared with heterogeneous composites, SPCs offer superior impact resistance, reduced weight, and enhanced recyclability while maintaining high mechanical strength.
However, production techniques for SPCs are challenging because the fiber and matrix material have similar melting temperatures. Work-around methods involving fiber hot compaction are time-consuming and expensive. Georgia Tech’s novel quasi-melt method involves use of a meso-state liquid that can maintain a fluidic state at a temperature well below the nominal melting temperature of the polymer. The quasi melt then combines with high-strength fibers to form an SPC with excellent mechanical properties.
- Highly effective: Facilitates increased fabrication of SPCs using a variety of processing techniques
- Simpler: Eliminates the need to develop a textile preform, which is necessary during fiber hot compaction processing
- Flexible: Is compatible with standard high-throughput melt processes for polymers and plastics
- Adaptable: Applies not only to quasi-melt extrusion, but also potentially to other melt processes including compression molding, injection molding, and calendaring
- Environmentally friendly: Uses a single polymer for enhanced recyclability
This technique can be used for mass producing SPCs using melt processing techniques (e.g., extrusion, compression molding, injection molding, and calendering).
Because of their synergistic properties, composite materials are particularly useful in advanced engineering applications. Heterogenous composites – where the matrix and reinforcement have different physical and chemical properties – can experience adhesion challenges, weakening their stability and mechanical properties. Because SPCs are one-component systems, and the matrix and reinforcement are of the same chemical composition, they offer high tensile strength and high impact strength. Georgia Tech’s manufacturing process enables the mass production of SPCs using a wide variety of melt processing techniques.
How It Works
The quasi melt is created by rapidly cooling—or supercooling—a normal polymer melt to a predetermined lower temperature where crystallization is largely suppressed. The concept of applying an undercooled melt in SPC processing involves introducing the fiber into a liquid matrix at a temperature well below the matrix melting temperature. Because the processing temperature is below the matrix melting temperature, and the fiber melting temperature is even higher than the matrix melting temperature—due to oriented crystals—the fibers added to the matrix will not melt and therefore will reinforce the matrix and form an SPC.
In studies, Georgia Tech researchers established a processing window of at least 25° C—from 135° C to 150° C —for processing polypropylene (PP) SPCs. Within this processing temperature window, high fluidity of the matrix PP was obtained without significantly reducing the fiber properties. The SPCs further exhibited higher tensile strengths and storage modulus over non-reinforced PP.
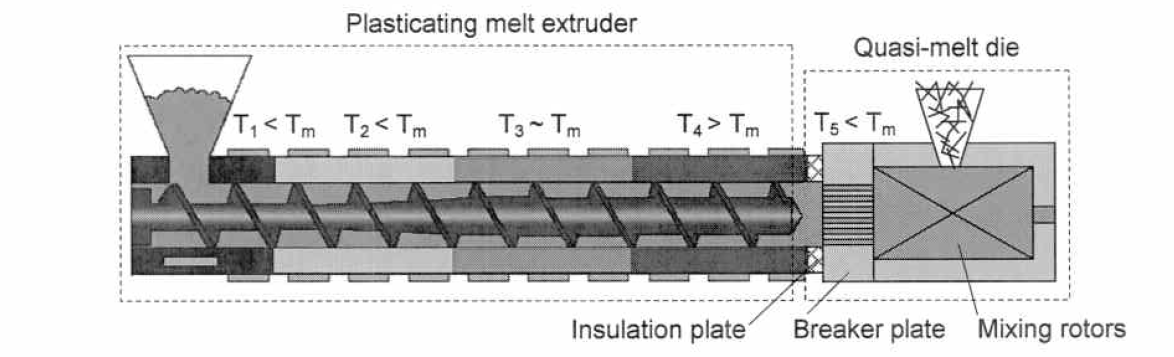
Schematic setup of quasi-melt extrusion for SPCs processing; Ti denotes the temperature of the ith zone.