Georgia Tech inventors have created piezoelectrically-transduced micromachined bulk acoustic resonators fabricated on a polycrystalline diamond film deposited on a carrier wafer or substrate. Consequently, the resonator can reach very high resonance frequencies while the frequency-determining dimension of the device stays in a range, comfortably feasible to fabricate using conventional photolithography and etching tools. The inherently high electromechanical coupling factor of the piezoelectric transducers results in low motional impedance resonators which are much easier to be interfaced with electronics. The lateral dimension of the resonating structure can be changed in order to alter the resonance frequency of the device. This feature enables realization of multiple frequency resonators on a single substrate meeting the requirements for emerging multi-band mixed-frequency wireless communication applications in a small size package. Depending on the piezoelectric material of choice and the substrate material the fabrication process could vary in some steps.
- Easy to use
- Customizable
- Compatible
- Etching
- Fabricating with conventional photolithography
Thin-film piezoelectric-on-silicon (TPoS) composite bulk 45 acoustic resonators (CBAR) were initially introduced by the present inventors to tackle the high motional impedance problem in micromachined resonators, while preserving high quality factors and frequencies. The large electro-mechanical coupling coefficient in a piezoelectrically-transduced resonator can potentially provide orders of magnitude lower motional impedance compared to a capacitive resonator at the same frequency. The underlying structural material in these devices improves the energy density, structural integrity, and resonance frequency.
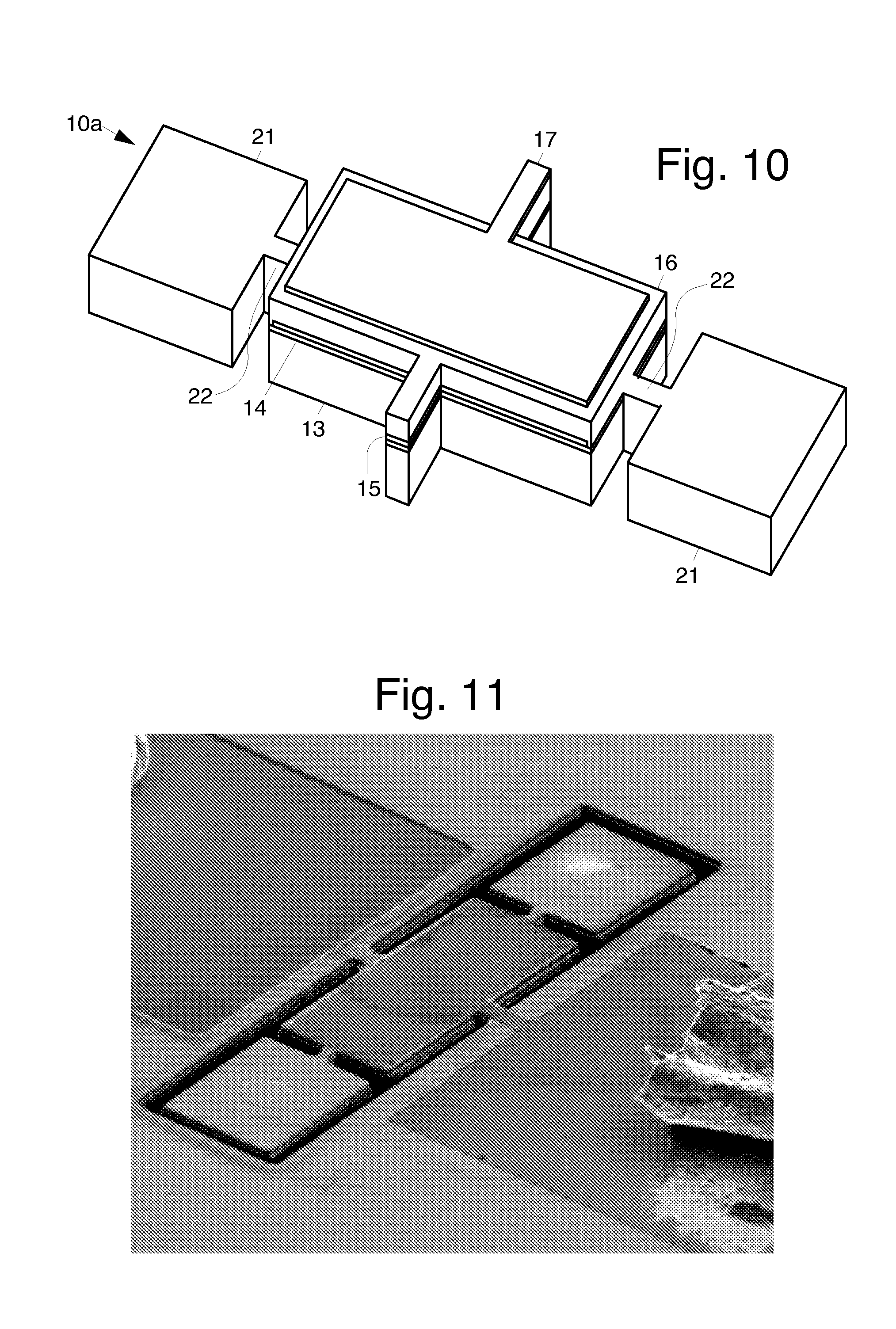