Ching Ping Wong, and Rongwei Zhang from the School of Materials Science and Engineering at Georgia Tech have developed an approach to prepare highly conductive polymer composites that involves in situ reduction of silver carboxylate on the surface of silver flakes by a flexible epoxy (diglycidyl ether of polypropylene glycol - DGEPG) to form highly reactive surface nano/submicron-sized particles; the in situ formed nano/submicron-sized particles facilitate the sintering between silver flakes during curing.
Sintering enables the formation of metallurgical joints and reduces or even eliminates the contact resistance among the conductive fillers, leading to highly conductive polymer composites. The reduction of silver flakes by DGEPG removed the surface lubricant and allowed the metallurgical joints and direct metal–metal contacts between the conductive fillers. This reduced or even eliminated the contact resistance effectively, enabling the preparation of flexible highly conductive polymer composites at a low temperature.
- The developed approach offers many advantages such as reduced materials cost
- Low processing temperature
- Compatible with low cost, flexible substrates such as paper and PET
- Simple processing
- Low viscosity of the formulated paste and low-cost jet dispensing technologies;
- Tunable mechanical properties
- Flexibility and high electrical conductivity.
This invention would be useful in the production of tightly assembled electronic packages, where electrical connections are required in three axes, such as cameras; electrical connections where the assembly is required to flex during its normal use, such as folding cell phones; and electrical connections between sub-assemblies to replace wire harnesses, which are heavier and bulkier, such as in batteries, cars, rockets and satellites.
The preparation of novel flexible highly conductive interconnect materials at relatively low temperatures (preferably 150°C or below) is essential for the future of low-cost flexible electronics. The popularity of flexible circuits and building electronic devices on flexible substrates requires the interconnect materials to be mechanically compliant and highly conductive. Low processing temperatures of the interconnect materials are also required to enable the wide use of low cost, flexible substrates such as paper and polyethylene terephthalate (PET).
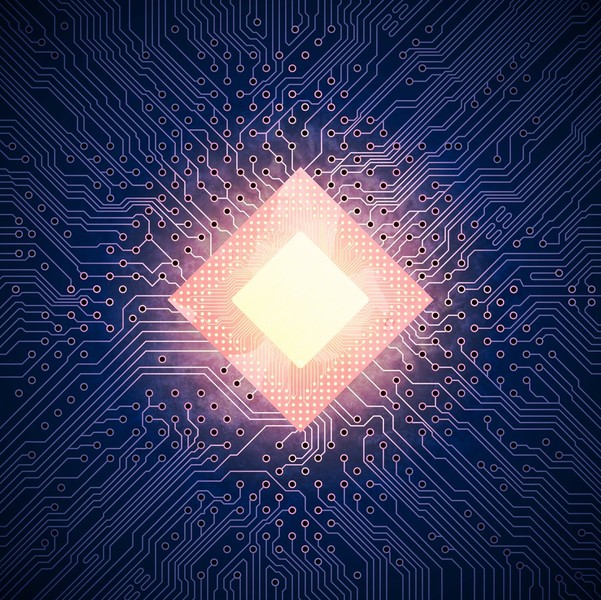