Georgia Tech inventors have developed a novel fabrication technique to impart anti-wetting properties to stainless steel without applying a coating, while still maintaining the integrity of the mechanical and thermal stability of the material. The process is a two-step electrochemical etching process comprised of sequentially low and high anodic potentials, resulting in the evolution of intrinsic hierarchical structures that impart enhanced anti-wetting properties to the stainless steel. Using dilute nitric acid as the electrolyte, the potentiostatic electrochemical etching is carried out at a low anodic potential to evolve intrinsic grain structures. A second step of potentiostatic etching step is performed at high anodic potential. The resulting surface shows a hierarchical structure composed of microscale intrinsic grains and enhanced nanoscale surface roughness. Further improvement in anti-wetting properties can be achieved through the application of a thin-film fluoropolymer layer resulting in a 160º static contact angle and roll-off angle of less than 20º.
- Utilizes intrinsic grain structures of stainless steel to modify surface wettability
- More efficient fluid transport and reduced energy consumption
- Does not require the deposition of additional coatings
- Maintains mechanical and thermal stability of the stainless steel.
- 2-step process occurring at room temperature.
- Enhanced heat transfer efficiency
- Commercial, industrial and military applications
- Antifouling coatings and reduced drag on ship hulls
- Power generation and desalination processes
- To create appliances and fixtures that are easier to keep clean
Stainless steel is an essential material in a variety of industries. It has superior corrosion resistance while retaining high mechanical strength. Understanding and controlling the wettability of stainless steel has significant value in imparting anti-fouling properties on surfaces, enhancing fluid transport, and facilitating surface cleaning.
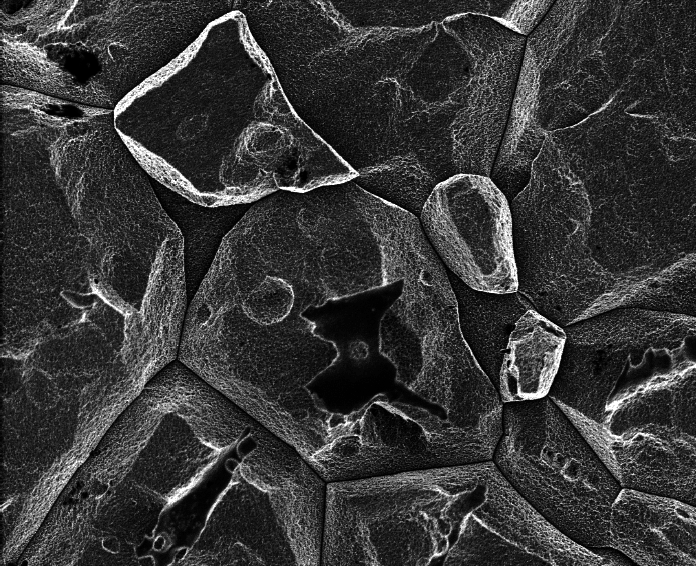