Georgia Tech inventors have developed a modified electrically conductive adhesive using innovative corrosion inhibitors such as amino acid and dicarboxylic acid. Proposed corrosion inhibitors can act as a barrier between the metal surface when forming a film over the metal surfaces, and therefore prevents the metal corrosion. The functional groups are either –NH2, which can form bonds by electron donation, or acidic groups, such as –COOH, which can provide the proton to catalyze the epoxy resin. Furthermore, the carboxylate ion can coordinate with the Sn ion and immobilize its migration property. By forming a barrier layer or a protection film on the Sn surface, or by forming a ring closure with Sn, the contact resistance of ECA's on the Sn and Sn alloy surface can be stabilized and the reliability of ECAs can be improved significantly.
- Efficiency — fuel flexibilty
- Cost effective — single-step solution and less expensive materials
- Lower operating temperature — clean production of electricity
- Improved operation — vibration-free and virtually noise-free
- Enhanced electro-catalytic activity — stability of the cathode
- Production of solid oxide fuel cells
- Power generation
- Transportation
- Military applications
With the phasing out of lead-bearing solders, electrically conductive adhesives (ECA's) have been identified as a environmentally friendly alternative to tin/lead (Sn/Pb) solders in electronic packaging applications. Unfortunately, unstable contact resistance on non-noble surfaces due to galvanic corrosion have been a critical issue and have prevented their wide applications.
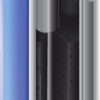