Need for robust SmallSat fluid management
Managing fluids without the assistance of gravity is a driving challenge for satellite manufacturers. The limited volume available in small satellites, or SmallSats has led to the adoption of conformal tank geometries, which complicates fluid management tasks. The use of two-phase saturated propellants creates additional challenges, resulting in traditional fluid management devices being unable to reliably meet the needs of these systems. Thus, there is a need for more reliable and efficient SmallSat propellant management systems and fluid management systems as a whole.
Three methods for SmallSat fluid positioning
Innovators at Georgia Tech have developed three SmallSat propellant management devices, or PMDs. These three approaches are thermomagnetic, thermocapillary, and thermo-dielectrophoretic PMDs, respectively. The new systems find application in saturated cold-gas propellants similar to several recent SmallSat missions, though they could be applied to any two-phase saturated fluid. In each device, propellant is vaporized or condensed through the addition or removal of heat to generate phase separation. Each of the three devices then uses magnetic, capillary, or dielectrophoretic forces to position the liquid and vapor phases of the fluid to allow extraction of a single phase from the system. All three systems offer a low size, weight, and power solution to fluid management that outperforms current technology in terms of reliability and efficiency.
- Safe positioning: Provides a way to reliably and efficiently control saturated propellants that compared to existing technology.
- Scalable: Can easily be scaled up and applied to different liquids and architectures.
- More reliable: Significantly enhances the reliability and efficiency of current positioning methods.
- SmallSat propellant management
- Sloshing and transfer of cryogenics in space
- Large spacecraft propellant management
- Biological sample management
- Low gravity phase separation
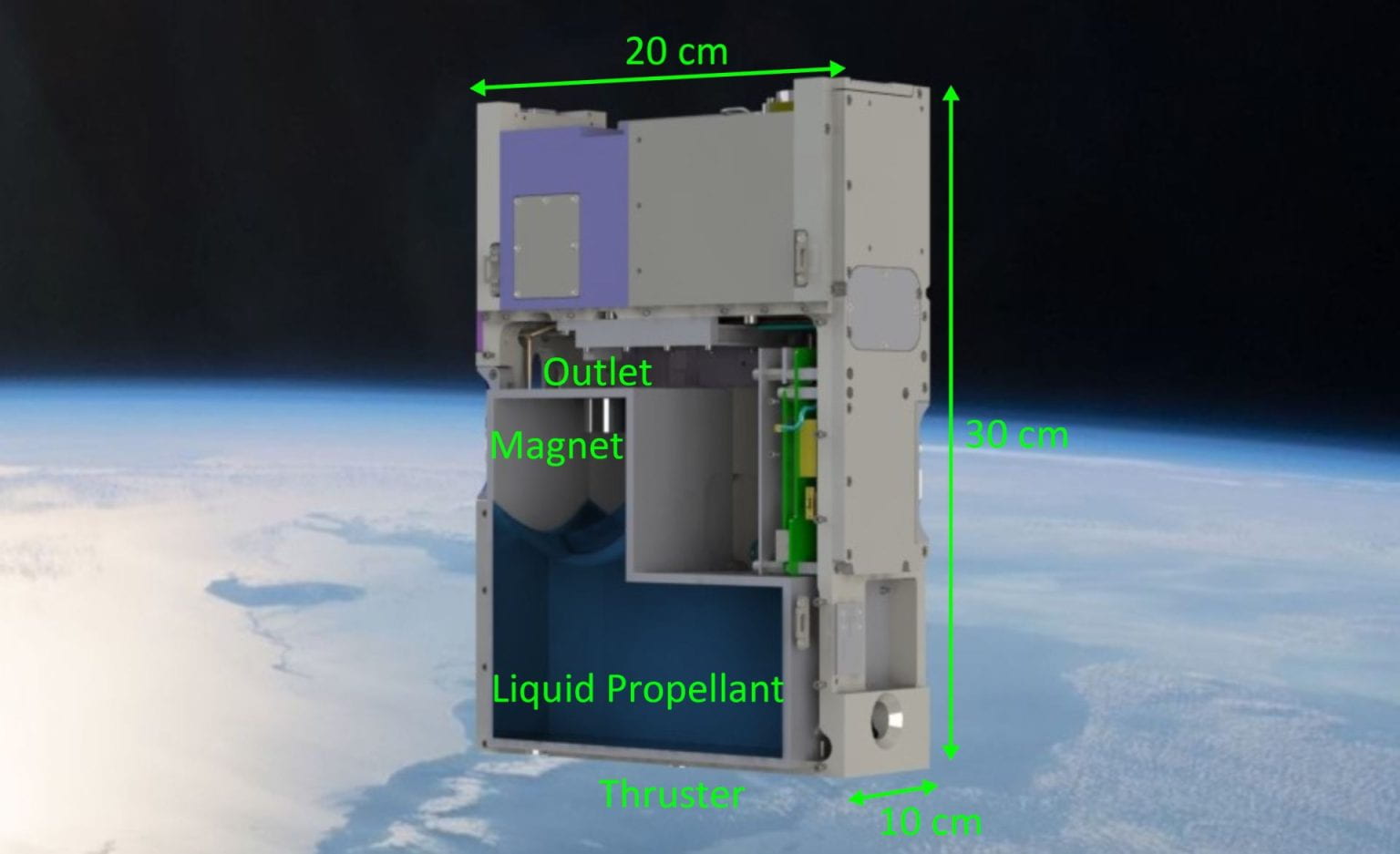
Conceptual representation of a magnetic positive positioning system on a CubeSat platform