This new fluid interface–supported printing (FISP) process for top-down stereolithography (SLA) 3D printing may reduce or even eliminate the need for sacrificial support structures that must be removed once the part is printed. Created by researchers at Georgia Tech, this process is faster, uses (and wastes) less resin, requires less human interaction to create a finished part, and produces a smoother finish. It also enables creation of more complex 3D structures than what is possible with current technology.
Current 3D printing processes create objects by depositing materials, usually in layers. The three-dimensional objects that are produced typically require sacrificial support structures. Removing the structures is time-consuming, costly, and often negatively affects the surface of the printed part. Georgia Tech’s FISP process has demonstrated printed overhangs of approximately 15 mm without sacrificial supports.
This technology offers several benefits associated with eliminating the need for sacrificial support structures, including:
- Reduced costs: Lowers costs by using less resin and requiring less user effort for support removal and post-processing
- Faster printing: Produces parts more quickly and easily
- Enhanced creation of complex geometries: Enhances the ability to create more detailed and complex structures using SLA 3D printing
- Better finishes: Streamlines mechanical printing process to produce parts with much smoother surfaces
- Enables Printing Multi-Functional Multi-Material Parts: Allows for adding different resins throughout the printing process to enable printing a complete part with various custom-tailored properties
This new method can be applied to existing commercial SLA 3D printing processes, particularly those that manufacture parts using ultraviolet (UV) light exposure above a resin base. These processes are used in the 3D printing of simple or complex:
- End products
- Rapid prototyped products
- Individual parts for both
SLA 3D printing is an additive manufacturing process utilizing a photocurable resin that requires sacrificial supporting structures to counteract the forces of gravity when the part being created has unsupported features, such as a cantilevered overhang. One drawback of the need for solid, sacrificial support structures is that printing these structures increases the print time and wastes valuable photosensitive resin. The support structures must be removed, requiring expensive manual labor and additional manufacturing time, and the resulting piece has a rough surface finish.
Processes to reduce the need for sacrificial support structures have been developed for other methods of additive manufacturing—such as fused deposition modeling. However, those techniques have other limitations and do not work for SLA printing, which enables the creation of much more detailed and complex structures.
Because SLA can print more complex parts, minimizing post-processing time and expense by eliminating the need for support structures would be a valuable addition.
How It Works
Georgia Tech’s FISP system consists of an optical setup positioned above a three-phase interface that consists of a transparent window, such as a fluorinated ethylene propylene (FEP) film; a thin layer of photosensitive resin; and a supporting fluid. A build platform is used to locate the part, and the transparent window allows UV light to pass through. Below the window rests the polymerization resin, which floats on top of the inert supporting fluid. The resin is polymerized (cured) by the optical system into the desired geometry on the build platform and is subsequently lowered into the supporting fluid. The FEP film provides a surface that the printed part can adhere to during curing.
The cured resin sits in the support fluid, which is tuned to match the density of the cured resin. This matched density enables the cured part to be neutrally buoyant and allows for the uncured resin to rest on the support fluid as well. The small difference in density between the cured and uncured resin minimizes the forces of gravity and buoyancy within the fluid, enabling a significant reduction in the need for support structures.
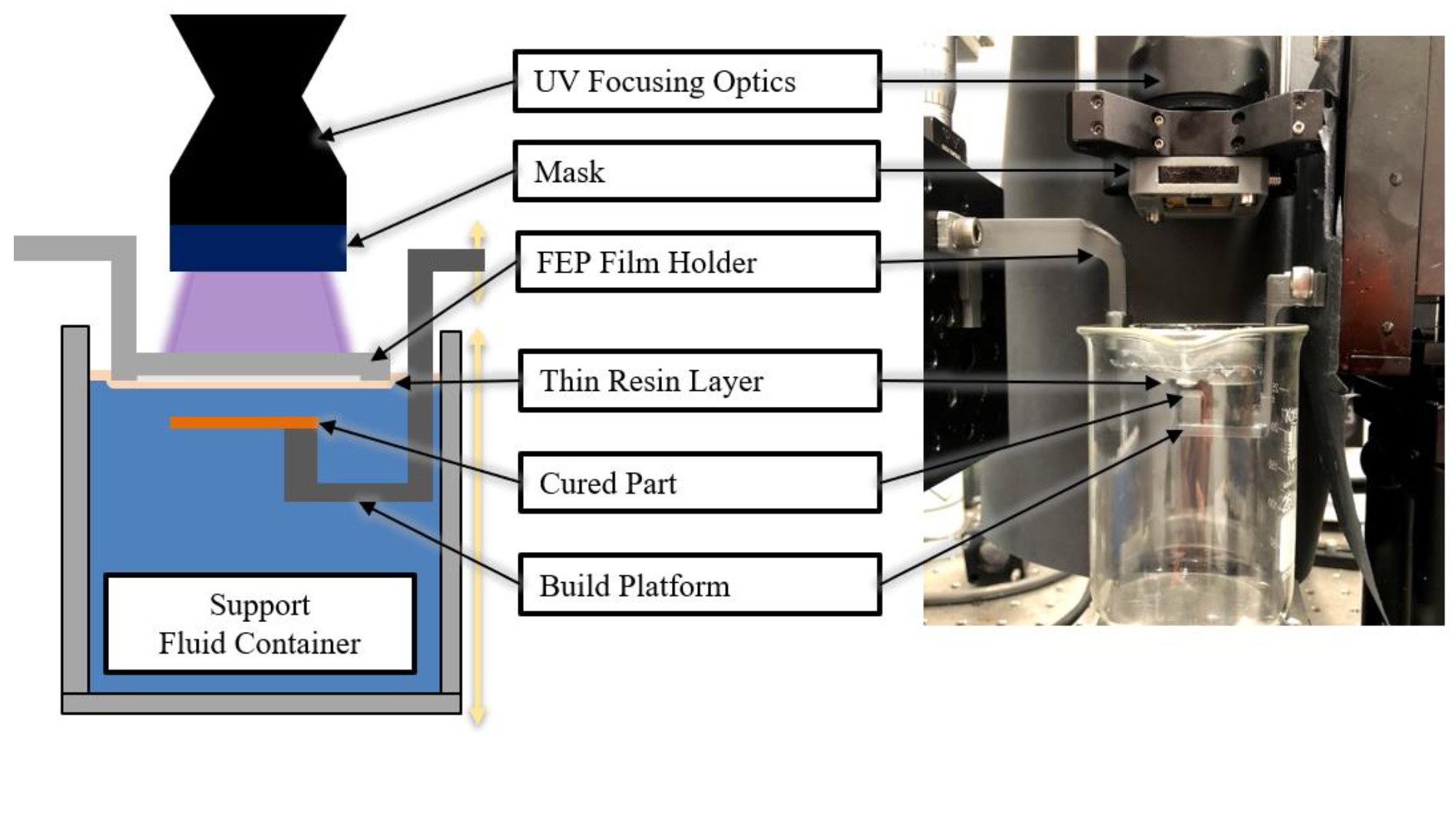
Setup of the fluid interface–supported printing system
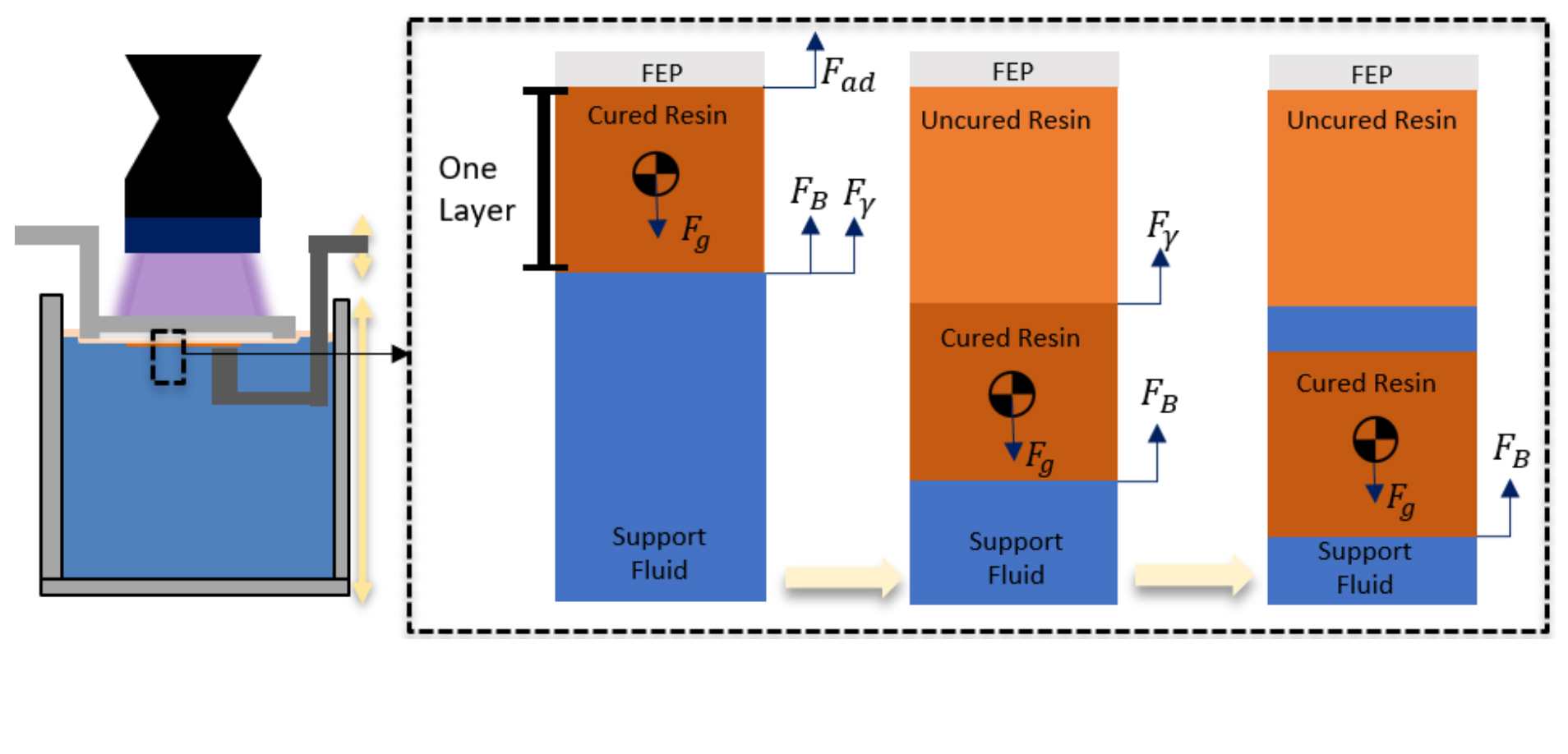
Diagram showing the forces associated with the removal of a cured layer from the FEP film