Inventors at Georgia Tech have developed a strategy based on time-scale separation and command shaping to reduce the powertrain noise, vibration, and harshness (NVH) associated with starting/restarting an ICE. By tailoring the torque profile provided by the electric machine (EM), the ICE can be started with minimal residual vibrations. The strategy uses a linear combination of constant and time-varying torque components. The time-varying portion of the torque is calculated using an analytical ICE model and a perturbation technique for separating scales and isolating the nonlinear response. Command shaping is then applied to the linear response governed by the remaining scale. Using this technique, effective mitigation of the residual vibrations was demonstrated in a simulation using mathematical models of the ICE and EM. Future work will include the development of a more extensive ICE model and experimental implementation of the concept.
- Uses a linear combination of constant and time-varying components to tailor the torque profile provided by the EM
- Results suggest a promising and straightforward technique for reducing vibrations during ICE starting/restarting
- Improve drive-ability and the overall driving experience, resulting in increased consumer acceptance of HEVs
- Approach can also be utilized to address other HEV-related drivability issues associated with powertrain mode changes
- Automotive industry- HEVs
- Hybrid power sources
- Engaging/disengaging of clutches
Fuel-efficient hybrid electric vehicles (HEVs) are becoming increasingly popular due to growing concerns over diminishing fuel supplies and increased global warming. However, vibrations from the start/restart of an internal combustion engine (ICE) in HEVs transmitted through the powertrain cause discomfort to the driver, which decreases the overall drivability of the vehicle. Presently, manufacturers use damping to reduce these vibrations, which is limited in its effectiveness. Alternative approaches that are more effective are desirable to improve drivability and increase consumer acceptance of HEVs.
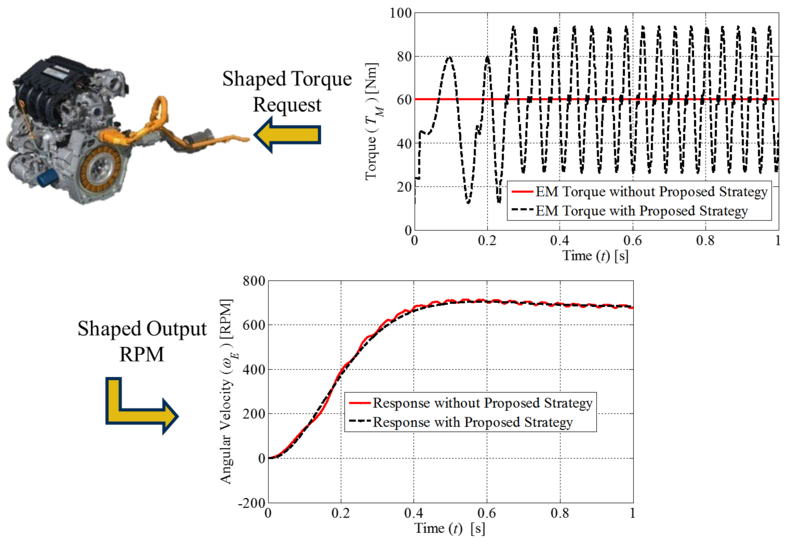