Georgia Tech inventors have developed methods using absorbent fiber composition. The goal of absorption processes is separation of fluid mixtures. This invention focuses on a matrix of absorbent fibers. Each fiber is comprised of an adsorbent material within a controlled porosity matrix. These adsorbent filled porous fibers can be formed into a module to enable controlled contact with a feed stream. As the feed stream is pushed through the modules, a cycle for the feed stream is created giving the stream cyclic exposure to the fibers. To achieve improved separation performance of the stream, the porous fibers permit favorable decoupling of the adsorption kinetics through the pressurization/depressurization dynamic process that occurs within the module. This is a novel approach that overcomes technical problems associated with the “binderless” small particle approach as well as with monolith module creation.
- Versatility
- Large scale separation
- Central bore
- Most axial fluid flow happens down bore instead of within porous medium
- Radial distribution occurs easily through fiber wall
- Possibility of multilayer fiber to quell shock waves in cycle
- Can be adapted to existing state-of-the-art capability in spinning fibers
- Diverse separation and absorption applications
- Production of 90% O2 from air
- Recovery 98% Hydrogen stream from a 33/67 mole ratio CH4/H2 feed
Control of porosity (e.g. by phase separation during fiber formation) is currently done for membranes with and without the presence of solid particles. Adapting this technology should allow excellent control of morphology within each individual fiber to decouple the axial pressure drop from the primary particle size as can be done in monoliths. This decoupling enables the use of longer beds and the production of compact high capacity processes. Unlike monolith production, fiber formation processes operate very reproducibly and as continuous economical steady state processes. Moreover, by adding parallel spinning stations, the process can be scaled to economically create large quantities of essentially identical fibers with whichever detailed morphology is desired for a specific optimum Rapid Pressure Swing Adsorption (RPSA) process. The nature of such fiber production processes will allow formation of relatively inexpensive fibers for module construction. Available membrane technology can be used to directly apply this invention to the formation of RPSA adsorbent beds.
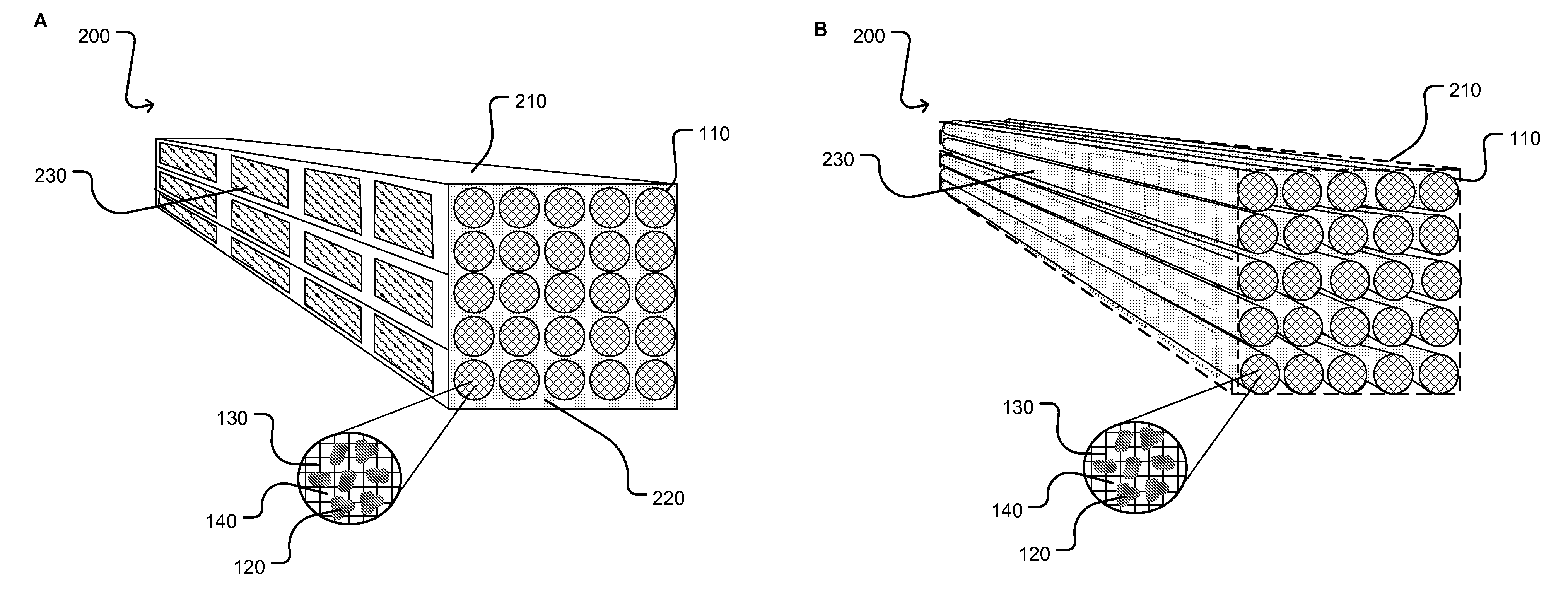