This process design enables production of high-purity ethylene and hydrogen without the need for energy-intensive carbon dioxide (CO2)/oxygen (O2) separation processes that add to the cost and complexity of other methods. Georgia Tech’s process for production of small molecules such as C2 hydrocarbons allows for efficient electrochemical reduction of CO2. This is accomplished using a downstream process that allows recycling of unreacted CO2 for a reaction with an intrinsically low single-pass conversion.
By eliminating the need for the most expensive methods of separation (cryogenic distillation or amine absorption, for example), the process significantly reduces overall energy requirements and therefore may also help to lower overall costs. Georgia Tech’s process can be customized to fit a variety of product streams, benefitting production processes that leverage upscaled electrochemical cells and optimized use of adsorbents.
- Efficient CO2 recycling: Allows for robust recycling of unreacted CO2 from an electrochemical cell
- Increased overall CO2 conversion: Features efficient use of recycling, enabling 100% theoretical atom conversion for this reaction with an intrinsically low CO2 conversion
- Customized deployment: Integrates with a wide variety of product streams
- Lower costs: Enables more cost-effective reduction of CO2 by eliminating the need for the most expensive and energy-intensive separation processes
Georgia Tech’s innovation describes a process flow for e-refinery which aims to convert CO2 and water to hydrocarbons using renewable energy. The process produces ethylene, syngas, acetic acid, and ethanol. It is broadly applicable to industries that use these products in their production processes.
Production of ethylene and hydrogen from CO2 is an important process for production of many petrochemical-based products such as plastics, paint adhesives, solvents, and more. However, most processes for electrochemical reduction of CO2 require CO2/O2 separation using cryogenic distillation and amine absorption. While industrially mature, these processes are energy intensive and lead to unsustainably high separation loads. (Cryogenic distillation alone consumes more than 90 percent of the separation heating load.)
Georgia Tech’s innovation offers an alternative to these methods by using adsorbates or membranes for separation of cathodic products to obtain ethylene and hydrogen with significantly less energy input. The process uses the mixture as an oxyfuel for combustion of biproducts of the reaction, rather than relying on inefficient thermal processes.
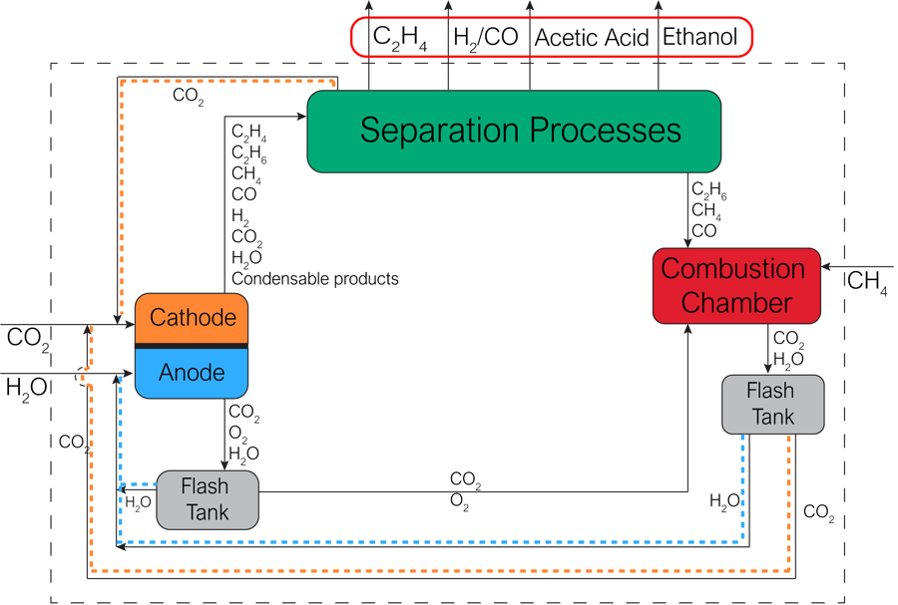
A diagram of Georgia Tech’s downstream process for electrochemical reduction of CO2