Need for high-power heat transport for small satellites
Recent improvements in solar power generation and energy storage have opened the door for high-power small satellite platforms with mission-enabling advances in electric propulsion, imaging payloads, and communications. As the power density grows, heat rejection and transport become increasingly critical. Body-mounted radiators are constrained by the limited spacecraft surface, making deployable alternatives a necessity for future missions. With deployable radiators comes the need for high-power heat transport across the spacecraft bus. Current solutions are insufficient as thermal straps are too massive for highly demanding applications, and heat pipes reach their limit for large heat fluxes.
MHD pump with liquid metal loop
Innovators at Georgia Tech have developed an active thermal control device consisting of a liquid metal loop powered by a magnetohydrodynamic, or MHD, pump. The device can satisfy the need for miniaturized and low-power active small satellite thermal systems by reducing the mass required per unit of transferred power by up to 60% compared to current thermal systems. The absence of moving parts and the high electric conductivity of the liquid metal precludes leaks and minimizes the pressure difference between the loop and external environment, reducing the mass of the pipes and facilitating the use of non-metallic lightweight fluid handling materials.
- Reliable: The absence of moving parts and low vapor pressure of the liquid result in enhanced reliability.
- Energy efficient: The absence of moving parts and high electric conductivity of the liquid result in minimal power consumption.
- Reduced volume and mass of heat exchangers: With thermal conductivity values two orders of magnitude above standard refrigerants, the volume and mass of heat exchangers located at the ends of the loop are reduced proportionally.
- Small and large satellite platforms
- Deep space missions that require more than 100W of power dissipation
- Surface cooling for reentry and hypersonic vehicles
- Spaceborne nuclear power heat management
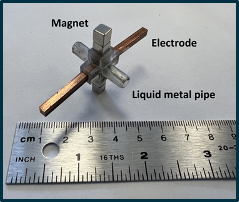
First MHD pump prototype
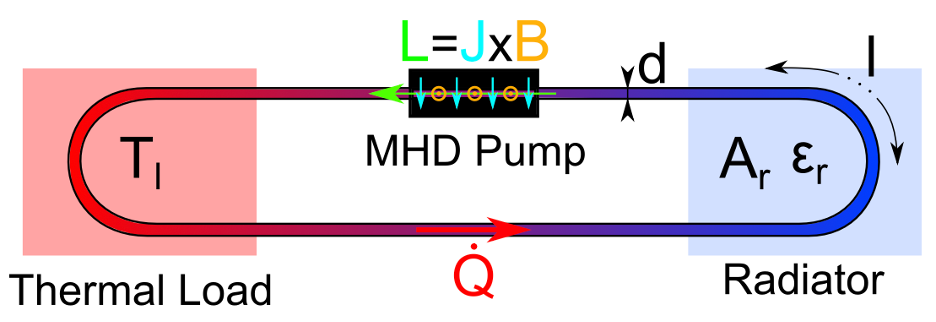
Schematic representation of the liquid metal loop
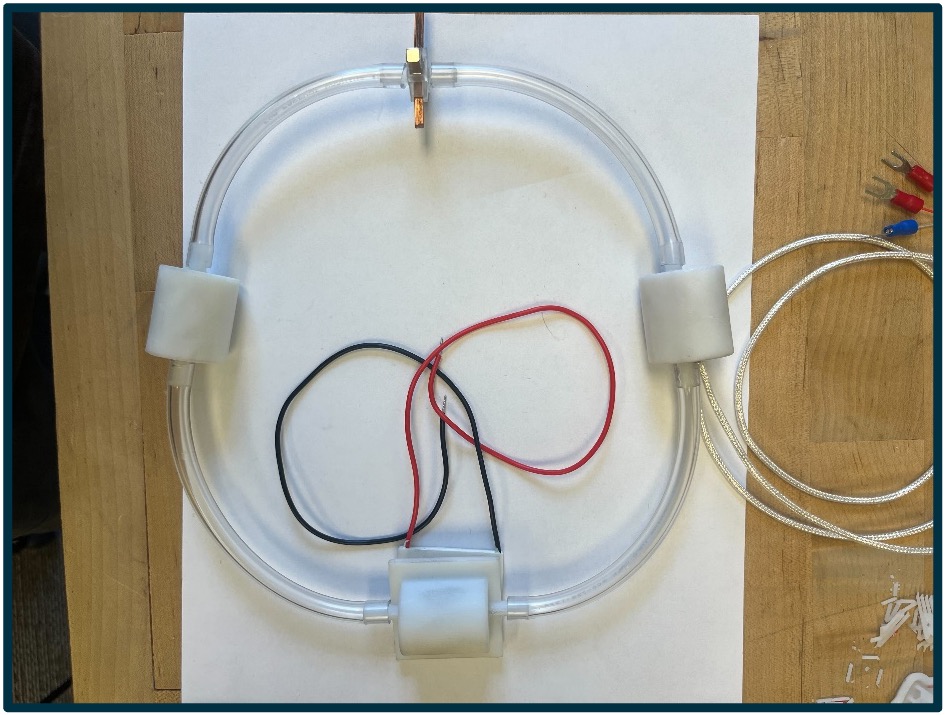
Laboratory loop prototype