Georgia Tech Inventors have discovered a process for incorporation of PCM into fibers through wet spinning-dry jet spinning of polymeric dopes. Microencapsulated PCM’s are first incorporated into a polymeric dope through a series of high powered sonication and mixing using an impeller. A "Prime Dope" with the remaining solvent and an equivalent fraction of polymer is then introduced and additional sonication and mixing steps are carried out. The dope is completed when the remaining required polymer is added and stirred until fully incorporated. Once all polymer has been incorporated, the completed dope is loaded into the spinning system, and allowed to degas for 12 hours to remove any air bubbles. Fibers are produced through extruding the dope through a spinneret through a low air gap, then through a water bath and unto a take up drum. Solvent exchange in water is carried out daily for 3 days.
- Improved thermally modulated fibers with high mass loading
- Implementing a heat/sink source directly into the fiber next to the sorbent material
- Enhanced pressure swing adsorption processes
- Efficient process
- Ability to incorporate phase change materials into fiber polymeric contactors
- Allows for other materials to be introduced "next to" the phase change materials
- Applied towards the production of thermally modulated fiber material
- Use with thermal protection systems
Phase change materials (PCMs) can store and release large amounts of energy to maintain constant temperature. Compared to insulation materials, they change phases and absorb and release a large amount of energy. Various industries, such as construction, transportation, commercial refrigeration, textiles, and packaging require efficient heating and cooling. Therefore, PCMs are expected to be environment-friendly and energy-efficient.
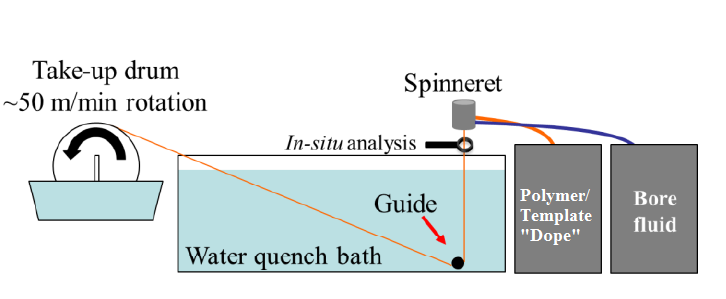
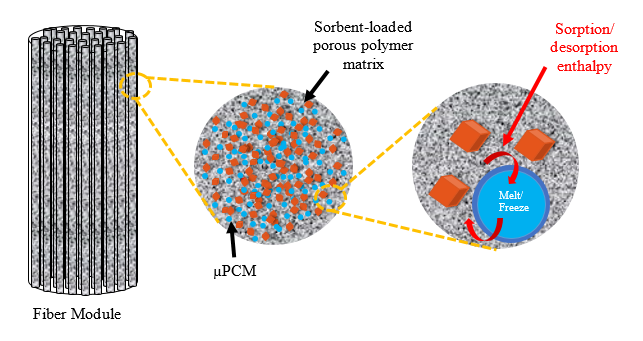