This anti-resonance system (ARS) and ARS blade design reduce vibrations and enable variable speed rotors (VSR) in helicopters and other flight vehicles, which improves efficiency. By incorporating a moving mass mechanism within the rotor blades, the system actively moves the resonance points—effectively removing the vibrations that come with VSR. The mass and location of the moving mass are carefully selected and controlled to effectively move the resonance points out of the rotor operating range. This reduces fatigue on the blade and other helicopter components. Variable speed rotors can improve speed and reduce power requirements. For example, reducing the rotor speed from 230 to 150 RPM at μN=0.2 led to a maximum power saving of 41.47%.
Located inside the blade, the sliding mass travels along the length of the blade on a rail and deforms with the blade. This changing location of mass alters the blade’s mass moment of inertia about its vertical axis, which changes the natural frequency of the blade. Varying the natural frequency, in turn, changes the resonance crossings. In this way, this new blade actively changes the location of its resonance points to prevent the vibrations that would typically be generated.
- High performance: Enables variable rotor speeds by significantly reducing resonance loads during transition from one rotor speed to another
- Agile: Reduces vibration by completely removing resonance points within the rotor operating range
- Energy efficient: Decreases power consumption by optimizing rotor speeds for different flight conditions
- Enabling: Demonstrates the potential to improve noise, speed, and power in helicopters
- Commercial and military helicopters manufacturers
- Urban air mobility companies
- Electric vertical take-off and landing vehicle companies
Most helicopters operate at a constant rotor speed and are tuned to operate at a safe distance from their resonance frequencies. This limits their efficiency and operating envelope (i.e., capabilities in terms of airspeed and load factor or altitude). While varying the speed of the rotor based on operating conditions can significantly improve the rotor’s performance and reduce power consumption, changing the rotor speed in current helicopter designs leads to vibration issues when a rotor passes through a resonance point. This can affect the vehicle’s aerodynamic performance, altitude, and speed.
The forces and moments acting on the blade and the hub increase significantly when a rotor passes through a resonance point. The longer a rotor takes to traverse a resonance region, the greater the resonance loads. These vibratory loads during rotor speed changes increase the fatigue of the blade and other helicopter components. Georgia Tech’s new ARS effectively moves the resonance point out of the rotor operating range.
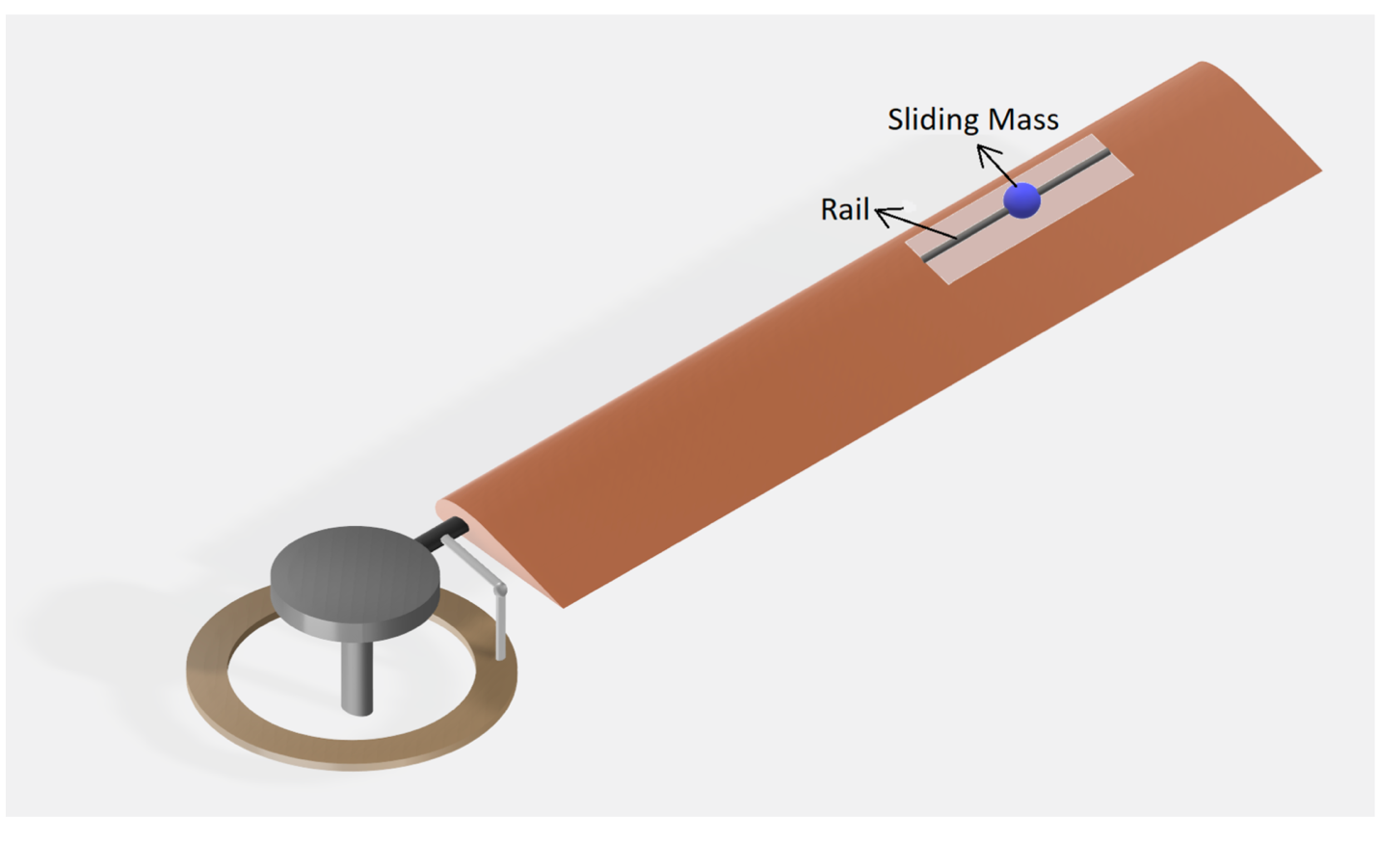
Hingeless blade with a sliding mass

Blade model with sliding point mass
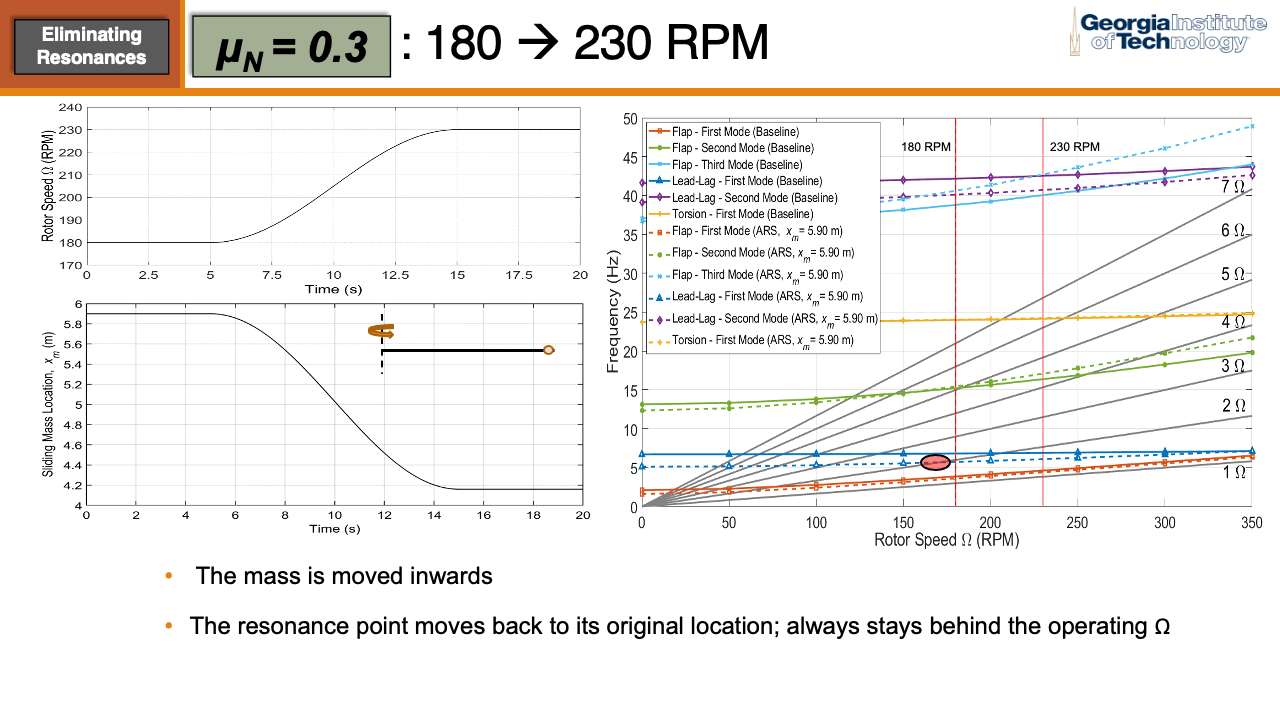
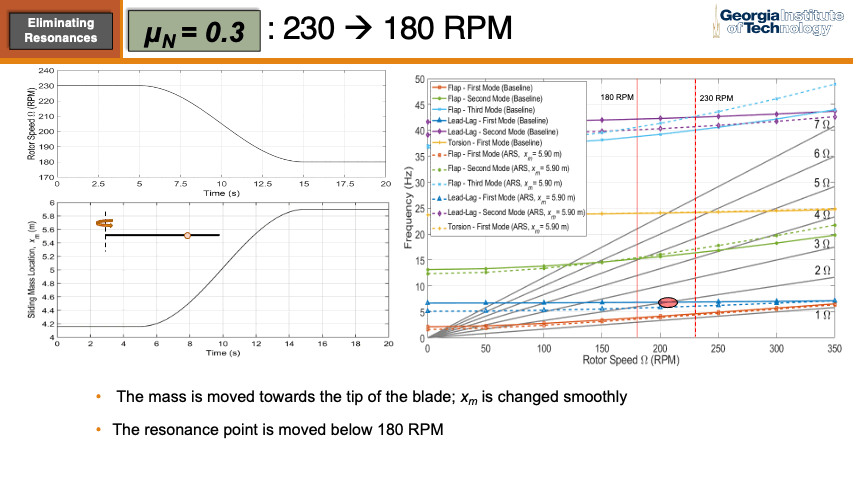