Inventors at Georgia Tech have proposed the use of a small percent of lightweight aggregate in the concrete mix to produce a clean, self-roughing surface. The lightweight aggregate floats to the surface and creates the roughened surface needed for bonding to the subsequent concrete placements. This self-roughening eliminates labor, safety concerns, and costs of manually roughing the cold joint surface. They have developed a concrete mix using lightweight aggregate which will satisfy code requirements for the construction of large concrete structures.
- Less time
- Less cost
- Reduced safety concerns
- No need for continuous concrete placements in 3rd generation modular construction
- Lightweight aggregates rise to surface producing a roughened surface
- Self-roughened concrete enhances bond between concrete lifts
- Vertical concrete construction
- Building and bridge construction
- Industrial facilities
- Underwater construction
- Precast concrete industry
Self-consolidating concrete (SCC) has been used in the construction industry for over 15 years. It is now being used in the construction of nuclear structures where concrete placements may be as high as 90 feet. The use of SCC allows the concrete placements to be made without internal vibration, which saves costs and time. Multiple placements ease construction but result in cold joints, which are commonly and successfully used in concrete construction. The bond between the placements depends on the surface roughness. The hardened surface of normal and self-consolidating concrete is typically smooth, which requires the surface to be roughened prior to the next placement. Raking the fresh surface to create roughness is typical for normal concrete but does not work with SCC. Jack hammering the hardened surface is required, which is expensive and may pose safety concerns.
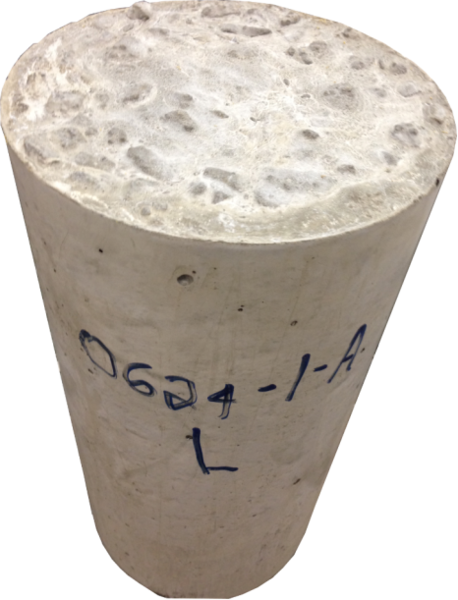
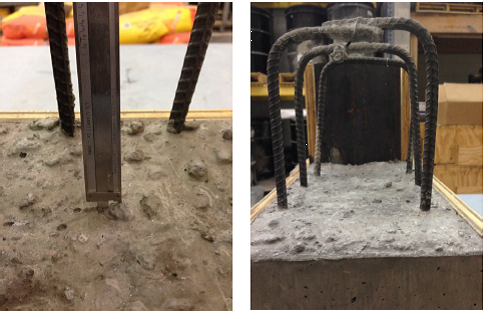